Born as an agreement between the three major automakers of the United States (Chrysler, General Motors and Ford), APQP is a methodology that brings together a series of techniques and procedures necessary to establish a quality plan that allows a product development (or service). according to the needs of the customers. APQP are the initials of Advanced Product Quality Planning. The three automotive firms founded in 1982 a non-profit organization called AIAG (Automotive Industry Action Group), which would then be coupled volunteers from other manufacturers, including non-US companies (such as Japanese Toyota, Nissan and Honda). The objective of this organization was to produce quality standards and establish common regulations for members. Today, AIAG’s role is much more complete, covering issues related to the supply chain of the automotive industry, the management of suppliers and corporate social responsibility, among others.
What is APQP?
It is a structured process to define the main characteristics for compliance with regulatory requirements and to achieve customer satisfaction. APQP includes methods and controls (ie, measurements, tests) that will be used in the design and production of a specific product or family of products (ie, parts, materials).
The APQP vary from one client to another, but generally we find the following:
- Review of the documentation and customer requirements
- Feasibility studies of the new requirements
- Synoptics of manufacture and control
- FMEA of the process
- Quality Control Plan
- Definition and development of manufacturing tools
- Products and services purchased
- Self-control guidelines, process parameters, packing guidelines
- Presentation of the initial samples
- PPAP dimensional reports, studies of process capacity and tools.
- Manufacture of the first series
- Approval and closing of APQP
What’s your objective?
Its objective is to produce a product quality plan that supports the development of the product or maintains it that meets the customer’s requirements.
Which industries apply this tool and why?
This tool was developed at the end of the 1980s by a commission of experts from the three major automobile manufacturers in the United States: Ford, General Motors and Chrysler.
These companies apply this tool when launching new products, and not only them, but also the entire auxiliary industry. That is, all companies that manufacture the different components of the car (suppliers) are required to apply this technique.
This tool is a requirement of the TS16949 standard, which is mandatory for those companies that want to supply large car companies.
ISO / TS 16949 is a technical specification based on ISO 9001, is the standard that defines the requirements of the quality system for the supply chain of the automotive industry.
The objective of ISO / TS 16949 is the development of a quality management system that offers continuous improvement, emphasizing the prevention of defects and the reduction of variations and waste in the automotive supply chain. The ISO / TS 16949 specification is applicable to the design / development, production and if applicable, installation and service of products related to the automotive sector.
The implementation of APQP is carried out in five well-defined phases:
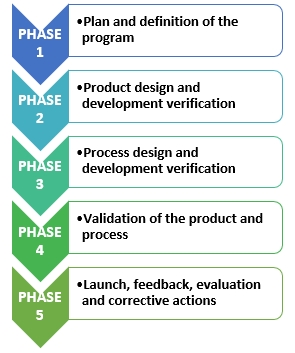
Phase 1: Plan and definition of the program for the development of the product.
In this phase the specific needs of the clients, their requirements and expectations about the product are gathered. The business plan is carried out and goals are set for both design and quality and reliability. The main tool of this phase is the QFD Matrices Deployment of the Product Quality Function or range of products in which 4 key dimensions are collected and integrated:
- Dimension “The Voice of the Customer”: are the functions and detailed specifications, one by one, that customers demand for the product.
- Dimension technical specifications and functions of the product: A robust, safe and reliable product design must be guaranteed. Reliability of its components, ease of maintenance and guarantee to meet the parameters established for its operation.
- Dimension of productive processes: What productive processes we have to manufacture the new product. What technological resources do we need and what should we invest in?
- Dimension reliability of the product during its useful life: The product must be easy to operate, reliable, with minimum annual maintenance and safe for the customer.
Phase 2: Product design and development verification
In the design phase APQP aims to know and evaluate the components and functions of the product in the design phase and ensure its reliability and compliance with the operating parameters. The most used tool is the AMFE Matrices for both the product and the production process, design verification, prototype reviews and materials and engineering specifications.
The AMFE Matrices allow to determine all the possible failure modes that may have the components of the product that affect the functions or generate unsafe situations for the clients.
Phase 3: Process design and development verification
In this phase, processes are designed, including everything related to plant layout, packaging, quality review of processes and products and process FMEA (PFMEA). The process instructions are also established, a plan for the analysis of the measurement systems is determined and a plan for the preliminary study of the capacity is made.
Phase 4: Validation of the product and process
In this Phase 4 the prototypes and pre-series of the products are made, delineating to the obligatory conditions of production and the necessary requirements within the industrial facilities.
- Production tests and efficiency indicators obtained.
- Evaluation of measurement systems.
- Preliminary study of the ability and capacity of the process: Run at Rate.
- Approval of parts and components in production (PPAP).
- Production control plan.
- Packaging evaluation.
- Quality plan. Proof of production validation.
Phase 5: Launch, feedback, evaluation and corrective actions
Industrialization begins and we focus on the reduction of the variability of both manual and capacitive production processes where Lean Manufacturing provides us with the necessary methods to analyze the indicators of productivity, capacity and quality of the product and its components. This phase covers:
- Reduction of the variability of process indicators. Eliminate the causes that generate variability and non-conformities.
- Customer satisfaction. Ensure that customers are satisfied with the product. Key customers test the pre-series of products providing ideas for improvement.
- Delivery and service. Guarantee and comply with the delivery dates promised to customers and provide the promised after sales service.
- Quality and control plans for the continuous improvement of the product and the process. Control Plan Methodology within industrial processes.
The combination of the Lean Project Methodology together with APQP and the analysis tools that both use allow to optimize the execution of the projects of new products from the design phase incorporating all the knowledge and lessons learned from other similar projects.