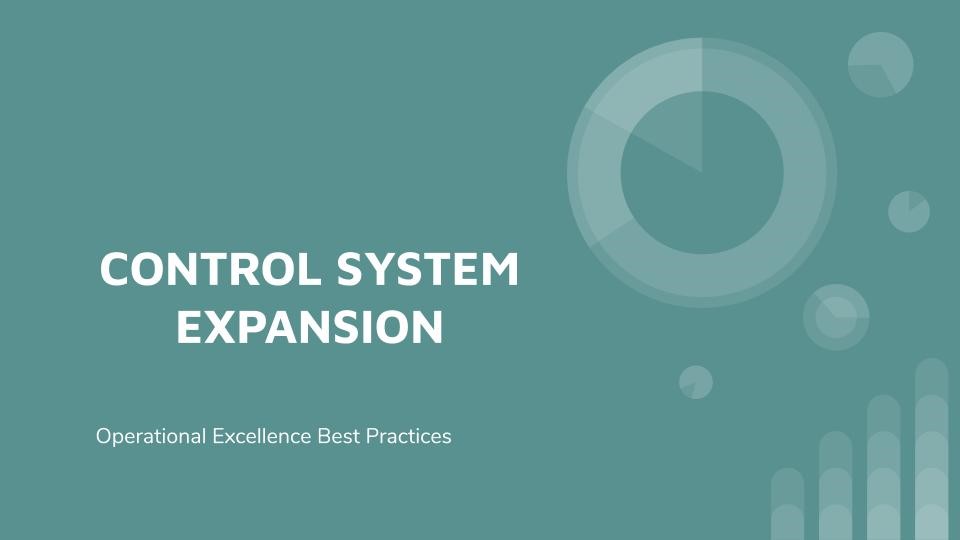
Industry 4.0 is an industrial phenomena that is changing the manufacturing landscape in a multitude of technically inspired ways. One such way is via the utilization of Control System Technologies. As the advent of the Industrial Internet of Things (IoT) emerges in the manufacturing realm, industrial processes are now less human controlled, and more machine controlled via process control technologies. All systems do need to be upgraded with time. As an operations manager, have you ever stopped to think about how old the control system at your facility is? If cellular phones are being upgraded annually, you must consider the fact that it will be important for the control system in your industrial facility to be up to date. With time, some parts are actually made obsolete by the manufacturer and it will be important for an organization to have an operating system that is “fixable”. If there are any problems, you’d want to ensure that you can replace the relevant parts.
Most industrial plant facilities contain field instruments integrated into a PLC controller based system. Operators engage with this system via an interface. In terms of control system parts, critical control system elements such as instruments, PLC controllers and circuitry tend to last a long time in instrument lifespans. With time however, the organization will need to upgrade the system to ensure that the system hardware is keeping up with the times. At best, try not to let your control system be more than a decade old. You won’t notice a problem till it occurs, so it will always be in your best interest to ensure that the system is up to standard. Knowing that your control system will need to be upgraded, how then does one proceed?
CONTROL SYSTEM UPGRADE
Control system upgrades are usually upgraded once the system:
- The business case for upgrading the system is validated. There are often times when a company will let a system run its full course and only consider upgrading the system when there are critical parts components that are no longer available from the supplier. Once an organization knows that their system is on the verge of obsolescence, they will then have no choice but to make that change.
- In an instance where there will be significant savings to be gleaned. One critical case for control system upgrades include scenarios such as power generation, where turbine back pressure control will be relevant to maximizing power generation. Since power is a high cost utility, implementing a system that will maximize what an organization can generate, and save the organization from power import will be a benefit to the organization. In a plant facility, there are numerous of these opportunities.
- Aside from hardware restriction, there can be instances where the software for the system is no longer supported. In a time where the cloud is going to be king, it will be important for an organization to understand how their operating systems for their plants will be able to withstand the changes in technology from a software perspective. Having a system with outdated software will place the organization at risk for cybersecurity threats. At this point in time, weaknesses in a system can cost the organization more than even the control system upgrade.
HOW TO UPGRADE
As with all upgrades, you can either go full hundred, or create within your operational plan a phased upgrade to your desired system. You don’t have to do everything at once, but if you take the time to do a small upgrade per unit time, you’ll then be able to eventually upgrade the entire system. Partial control system upgrades can facilitate the replacement of unit components within a system. With changes like this, there can be integration issues, so ensure that the change won’t cause any system shifts. In the right situation, this can be the ideal situation. Components you can replace if this is ideal include the PLC controller, field instruments and any wiring that needs to be changed.
If this method can’t work for your system, take the plunge and upgrade the entire system or entire systems in departments in a phased manner. A phased upgrade must be done if the control system is an obsolete one. Legacy systems are in this category.
Once completed, the organization can take advantage of the efficiency that comes with a new system. Energy efficiency, plant agility and management will be achieved. With Industry 4.0 taking over, as an organization, take the time to ensure that all the tools are up to the industrial standard. Competitive advantage is a moving advantage. You want to ensure that you are utilizing your tools to manage your resources and flows to achieve the optimum performance. Chemical process control is the key to process efficiency.