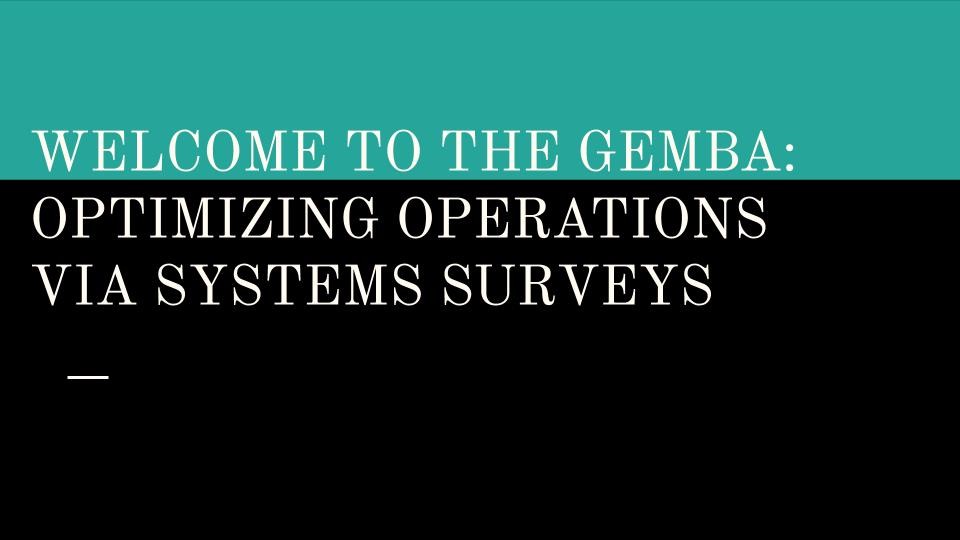
Industry 4.0 is changing the way that we live our industrial lives. As an intelligent interconnection of machines and processes, we can definitely look forward to the improvement of systems that are information and communication rich. Fusing our digital lives with our industrial processes will enable the achievement of smart value chains that are just in time enabled. The ability to satisfy our customers will be enabled by our responsive systems.
Industrial systems during an evolution such as ours are always open to room for improvement. One such way to identify how our system can be optimized, is via the utilization of tools such as Gemba. Automation, and process control doesn’t mean that the plant will all of a sudden be able to run itself, and that we’ll all be able to sip martinis and view the control charts from a beach. There is still a need for human intervention in industrial processes.
One way to accomplish the objective of ensuring that your facility is operating at peak, is via the utilization of Gemba walks. In our operations, the aim is to ensure that all is operating smoothly. When leaders are able to navigate the plant environment and see it in action, the ability to see clearly how the process and value creation is executed will be accomplished. The only way to see room for improvement, is to actually see what already is there. Where there are flaws, the action plan can then be created for rectification.
In 2020, where automation and digital information flow will be relevant for our operations, it will be important for organizations to ensure that the opportunities found during Gemba walks, be incorporated into an Industry 4.0 based strategy.
How Is Gemba Achieved?
The Gemba exercise is usually scheduled into the weekly routine of an industrial organization. What gets managed, and monitored, is what will be the focus of an organization. As best as possible, ensure that the organization has a Gemba champion, with a checklist of the areas that must be audited. A system of entry of queries for completion will also be managed by the Gemba champion, to ensure that they are actually accomplished.
1 – Organise a Team
All missions require a team to accomplish them. Within the management realm, identify the persons who will be best suitable for the Gemba activity. At best, include a manager or a supervisor, who can implement change if a problem is identified. The Gemba champion will identify the critical zones in the department that will need to be focused on. For each week, the team members will then take the time to walk the designated area and ensure that all is well in that zone. Are there items that are missing? Could you do with brighter lighting in that area? Is the air conditioning working in an area that is very hot on your plant? Are all your pedestrian crossings painted? All of this information will be critical to ensuring that your operating standards are at their peak.
2 – Utilize a Gemba Template
In the industrial realm, what is standardized is always king to ensuring that each team is conducting the same audits per unit time. For the designated areas that are identified in the department, ensure that the template for that audit is readily available. Ideally, in your department’s conference room, you will have a pocket that has pre-printed audit sheets that your team can use. Alternately, you can automate your Gemba process and utilize an activated spreadsheet, that enables you to complete the audit on a tablet, and have the relevant data collated in your system behind the scenes. In the survey, you will then take the time to ensure that the process is operating at peak. Gemba surveys do have weightings per question that you will tally. For your quality standards, you can ensure that you’re above 80% just to ensure that the operations are as close to design as possible.
For further observation and for the documentation process, you can actually go through the process of utilizing your phones to record a video of a discrepancy, or even to take pictures of scenarios that are ideal, or can be improved.
3 – Ensure that you are focused on a KPI
In your organizations value stream, there will be key areas that you’ll be looking towards optimizing. These can include the improvement of quality, of costs and even of the time that things take to complete. Operational value streams often help to identify what will be critical in your team’s weekly Gemba audits. On a quarterly basis, sit with your organizational team to ensure that relevant processes and work areas are being accounted for in your Gemba audit. If you operate a sample laboratory for instance, ensure that you have a library where you keep your raw material and finished product samples in an organized systematic manner that will be understandable by the employees.
4 – Process Orientation
One very important thing to note about organizations is that people will always move. With time, employees will get promoted, and someone new will come in to take their place. When new employees come into an organization, it is always important to ensure that they are oriented with the system and keep it operational. With time, as new employees observe that their leadership cares about the process and how it is managed, they too will take the time to ensure that the process is in order. Employees will understand why and how things are done in a particular way, to preserve the quality of the organization.
Gemba or the field walks is the key to ensuring that the plant operates at its peak. There is always room for improvement, and by taking the initiative to actually do things, you’ll find your organization on a path to growth. Via the advent of Industry 4.0, you can find systems that will bring the desired objectives.