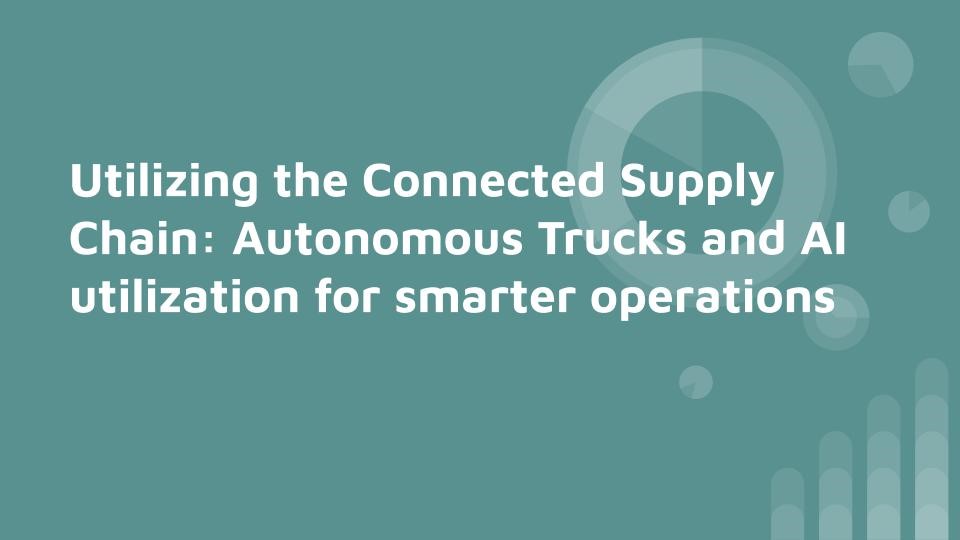
“Deep learning will revolutionize supply chain automation. Deep learning is what makes driverless vehicles possible.” – Dave Waters
The future of logistics is here and waiting to be deployed. Automation is the key to the establishment of a “connected supply chain”. As the current pandemic has taught us, we must be prepared for an autonomous future. With the potential for disruptions in the supplier and production networks due to any conditions from weather related phenomena, health related scares, and even market volatility, industrial manufacturers must be read for change. The best way to get there is to utilize all the perks of Industry 4.0 and optimizing the existing processes.
What Impacts Supply Chains?
Supply chains are very complex mechanisms that facilitate the distribution of items from a supplier to its customer base. With various interconnected elements in the transportation network, there must be some element of synchronicity between the involved parties. When determining how to engage all the different elements of the supply chain members such as suppliers, logistics service providers, freight forwarders and other critical process partners must be in the communication loop.
Communication in the supply chain is critical to ensuring that there is transparency in the supply chain. In the current global regime where fluctuations exist in the market demand, having key operational plans will be the way that organizations will be able to thrive. Just In Time Operations will no longer be a pipe dream, it will have to be a reality. Having a clear understanding of how the production forecast will be, will ensure that there is an appropriate operational, tactical and even strategic plan in place. With an autonomous supply chain in progress, the relevant systems can communicate with each other, and ensure smooth operations. Process transparency has to be a top priority to ensure success in the supply chain management.
Process Optimization Case Study
In the manufacturing of industrial process parts per instance, it will be critical to ensure that you are focusing on the primary goals of system optimization in your supply chain. With the aim to establish and maintain a Connected Supply Chain, it will be critical for you to ensure that certain key tenets are upheld.
- Process Transparency: This tenet is key to ensuring that the relevant notifications are given to a supply and customer team. In the industrial realm, the majority of processes are continuous, and the aim is to ensure that there is a balance of inflow and outflow. If there’s a decrease or an increase of any parameter, the supply chain will be affected by this change. If the suppliers are aware that their customer needs less of a product, the relevant aspect of the transportation of that product can be forwarded to the freight team, who can then adjust the delivery.
- Information Aggregation: Data is key to process optimization and process stability. Via the collection of information from systems such as process control systems, parameters such as quality enhancers can be tracked. Where deliveries are also concerned, it will be possible for the team to track products from generation to supply. Batch quality will be easily tracked.
- Higher Visibility: With every element of the supply chain interconnected by computing systems, suppliers and freight forwarders will be able to “see’ each other. By knowing what is happening in the supply chain, all elements, or the relevant portions of the system can then respond.
- Analysis Options: Systems have varying elements of performance. From the generated data, it will be possible for teams to determine key terms like the average performance of a system, the standard deviation, production range, takt time and other critical process parameters. All these elements and more can be utilized in order to optimize supply chain optimizations.
- Forecast and Simulation Options: With processes, before, during and after production it will be possible to forecast and simulate the operational performance. The creation of what if scenarios, indicating the best case and even alternative paths during downtimes can be determined from the computer simulations. With the differing cases, the impact on the supply chain can also be determined. If all teams are aware of the changes, they can adapt.
Utilizing all of this information, all the aspects of the supply chain can then be factored into the integrated system. From the user perspective, when you order a package from an entity like Amazon, you are able to actually trace the product from the warehouse through the shipping process. Manufacturers do benefit from their own tracking mechanisms from the data gathering phases in production, all the way through the shipping from their warehouses to their final customers who may be another industrial site.With predictive functions, it will be possible for future production scenarios to be “seen” by all systems. The production schedule, will therefore always be known, and not necessarily be calculated by operations managers.
Knowing the variances that are analyzed and forecasted, the appropriate quantities of materials can then flow through the production system. Billing will also be dealt with automatically via the interconnected ERP systems of each entity in the supply chain. Variations from the norm, will be allotted for via the utilization of system alarms. With the appropriate human entry into a computer interface, any relevant changes can be made, if the system is not on auto.
The benefits of a connected supply chain are immense, and only becoming more relevant now. With the various advances in industrial process technology, a smooth approach to supply chain optimization is now possible.
SELF DRIVING TRUCKS
In the wake of automation, self driving trucks are the future of freight. With various companies in the process of developing such technologies, eventually we will reach a stage in process optimization where driverless trucks will bridge the gap between suppliers and customers. With higher efficiency and reduced costs, companies that ship freight, can improve their bottom line.