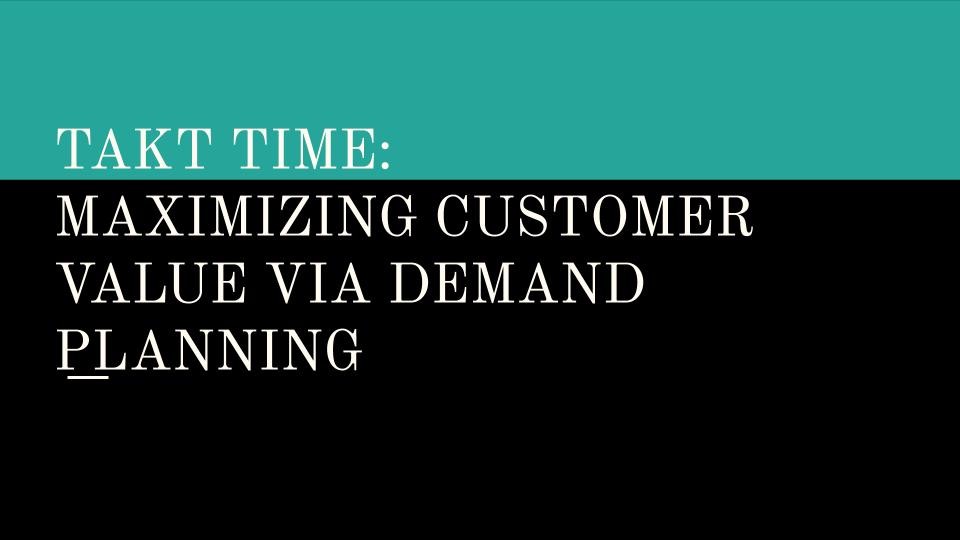
Lean Management in a 2020 lowered production era, is one that will be able to keep plants sustainable. As a system that will pull an organization forward, it is always a good idea to ensure that the feedback loop that keeps the organizations progressing is in place despite the global condition, and despite the number of customers that the organization has.
In some industrial spheres, such as the car manufacturing industry, pull systems are utilized to stop an operational flow that is in progress, in order to ensure that the relevant fixes to the spotted discrepancy have been identified. Pull systems empower the employees who utilize them, and ensure that quality work is sustained in the process of delivering products to customers. The ideal is to have a continuous flow of work, but where possible, the induction of a pause will be warranted. There will be an average performance, but in those instances where there’s a deviation, the team can utilize the appropriate levers to accomplish the objective.
How do you know what is normal in an operation? By the utilization of the critical metrics. These metrics include the definition of parameters such as takt time, that will ensure that there is an organizational standard where the process timing of particular activities is concerned.
What is Takt Time?
As one of those wonderful operational terms that we all come to eventually love, takt time is the rate at which an organization needs to complete a product for customer delivery. It is a balance of the inflow of customer demand, to the output. For continuous operations, you will have to balance the demand with the supply. If the order rate is equal to one per 7 hours, the organization will have to ensure that it is delivering that amount or else there will be a backlog of deliveries. The takt time is also defined as a sell rate, and determines how best the organization will have to optimize its operations if it’s already at peak capacity.
Just In Time operations are still relevant in 2020, and it will be important for an organization to ensure that it is able to keep things flowing. As the pulse of an organization, it is one of those parameters that is a must know for all production personnel. In 2020, with the global economy paused for a few months, you’ll definitely notice a shift in this parameter. The key is to keep it constant, and then allow the parameter to grow as life stabilizes.
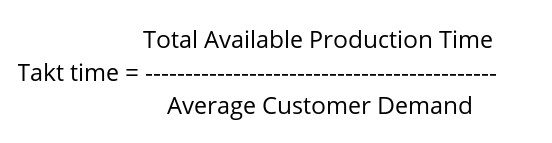
For your organization, you can take the time to have your process engineers look at your operational data, and then determine the mean of each of the parameters of production time and average customer demand. This will give you statistical accuracy, and also allow you to ensure that you are in a position where your organization is able to gauge its performance based on actual data, versus just working from the data that is on an equipment’s name plate.
With time, there are process shifts and it’s always important for a company to know how it performs with the changes in production levels. For instance, it is quite possible that there may be production limitations downstream, which can prevent a production operation to be operating at 80% versus 100%. All of these factors will affect your actual takt time, and utilizing the proper process data will ensure that you are being realistic. Calculate the takt time for productive periods and you’ll have the true picture.
With the advent of Industry 4.0 technology, you are now in a position to have a more accurate picture of your takt time, if you haven’t already calculated this parameter. If your organization manufactures silicon boards for the computer industry, you can calculate the takt time for your organization. For this operation note:
- Operational hours: If you’re continuous this will be seven days per week
- Number of shifts: There will be changes in activity across shifts, so filter them out and check the differences
- Clean any breaks from your data: These will usually appear as troughs in your graphs. Filter data, organize in order of size and remove the smallest numbers on the data flow.
- Number of orders: Are you receiving 1000 orders per week on average?
From the actual data, calculate the realistic takt time. What this will do, is enable you to know exactly where you are. From that baseline, you can then take the time and build yourself forward. The power of industry 4.0 is that it will give you the tools that will enable you to live your best operational life. If you’re not at peak, find the root cause, identify your target, and work towards it.