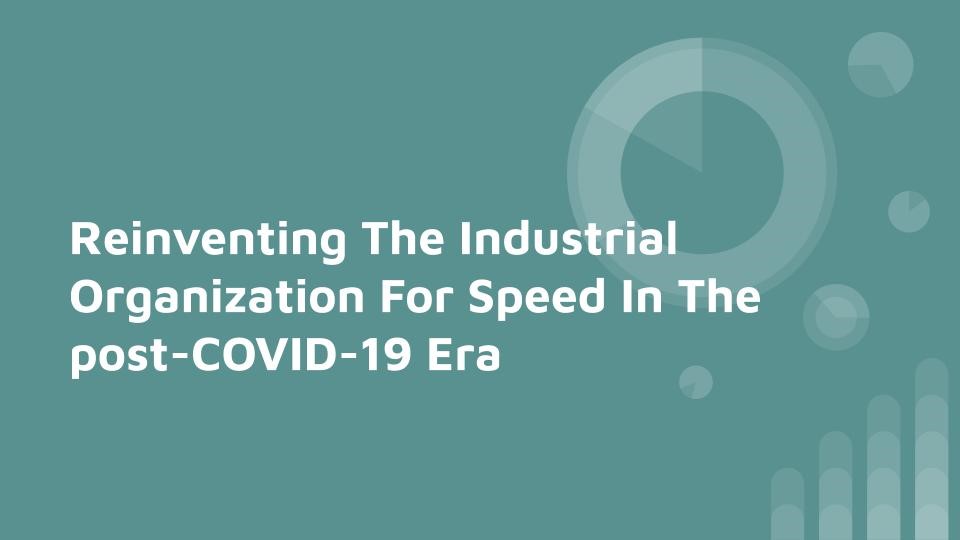
In the new manufacturing world, data and AI will rule. Technology is making industrial waves in ways that we never anticipated before. From advanced robotics, computer vision, to lights out manufacturing, technology is the wave of the industrial future. Technology is definitely making an impact on every step of the industrial manufacturing process. Where we are headed as an industrial nation is the Lights Out Manufacturing era, where factories can operate autonomously and require no human presence. Without human presence, and embedded with sensors, robots can actually function properly in the dark. Competitive advantage is a moving target that must be maintained, and technologies like lights out manufacturing are the way to go. Industrial organizations are taking various steps to optimize their processes via the utilization of tools such as advanced robotics, computer vision and even fog computing.
As futuristic as it sounds, “lights-out” factories have existed since 2001, with the FANUC factory in Japan being a prime example of such an engineering marvel. The plant can operate for up to one full month without human intervention. In a world where we’re now plagued with phenomena like pandemics, we can guarantee production with the advent of a “lights-out” factory.
The aim of business, even with a social consciousness embedded, is to make a profit. A business analysis conducted by the consulting firm Accenture, has indicated that with the advent of “lights-out” operations, industrial profit margins can increase by up to 39%. This will be impacted by the fact that overhead costs for labour and utilities will be reduced by robotic operations. Factories are becoming smarter thanks to the advent of Industry 4.0. With the advent of technologies such as Big Data, Advanced Process Control and even extensive sensor utilization in the factory environment, it is possible to see the plant’s performance and optimize it where necessary for production and safety purposes.
-
Analytics & Intelligence
Predictive manufacturing is the key to industrial process optimization. This phenomenon is made possible by the advent of data analytics. With data, process engineers and process control engineers are able to generate industrial models that are indicative of the current baseline operations of a facility, and identify room for improvement. With Analytics and Foresight available, more just in time operations can occur, and also maintenance scheduling can be optimized.
Downtime is a costly operation, costing organizations up to $647B a year. When unplanned, it can cost even more. Knowing that the majority of factories are not operating at their peak, this tool will enhance the ability of industrial plants to see their true performance and make changes.
Industry 4.0 is still in its prime, and is expected to mature in the next twenty years. With the current phase of digitization, the future will then involve the transition from predictive maintenance to true predictive intelligence.
A. AI & IoT Platforms:
Predictive Analytics is dependent on the availability of information. Industrial organizations are able to access this information via the availability of sensors in the field, that generate process data and submit them to industrial servers for storage. There are a few industrial companies that are leading the way with respect to the ability of industrial plants to gather and process industrial data. Samsara, Uptake, Oden and Augury are able to successfully provide Industrial Internet of Things solutions, and generate integrated systems of hardware, software and cloud storage. With the generated data, the appropriate Artificial Intelligence (AI) and analytics will be available for organizations to make appropriate decisions on.
To supplement any additional gaps that the aforementioned companies may miss, companies like Palantir can fill the data analytics gaps. The organization has an ability to utilize its SaaS platform to integrate process data, and provide forecasting information.
B. AI computing solutions: Edge tech & Semiconductors:
With no pun intended, there are technologies that enable computing to be done on the “edge”. In this instance, we define this edge as the industrial grounds themselves. Current and previous technologies were designed in such a way that information would be sent to a central processor and information generated from this process data. Currently, thanks to the advent of advancing innovation, processing close to the sensor sites is now possible. In small devices such as IOT sensors, and even flying vehicles like drones, they can process their data independently of the cloud. Pioneers in this field of edge computing include organizations such as Edge Analytics, Saguna Networks, Foghorn systems, Horizon Robotics, Oden Technologies, SenseTime and IoTech.
C. Industrial Cyber Security
The Industrial Internet of Things (IIOT) is based on the framework of wireless fidelity technology. While the gain to industrial processes is the advantage of process information in real time, the risk to the technology is the fact that wireless systems are more vulnerable to cyber attacks. Industrial audits have indicated that the manufacturing industry is at most risk for cyber attack. This could be due to the proprietary nature of operations, and the heavy competition that can somehow develop in certain industries like computing. To ensure that factories achieve their operations objectives and also manage their system boundaries to prevent breaches, careful attention will have to be paid by the organizations IT departments. Engagement with cybersecurity experts on a regular basis, will enable such an objective to be met. Claroty is a major player in this field and is able to protect industrial control networks from cybersecurity breaches.
-
Simulation & Software-defined Manufacturing
Research and Development is increasingly a digital activity. When ROI is uncertain, you want to ensure that as an organization you are able to understand and optimize your current systems. With tools such as data processing and simulation tools, an organization can fully understand the operations of their facility. Future design tweaks and process performance can then be operated on the digital twin of the factory, before its physical twin is actually built in reality. Productivity increases have been noted as a result of Design, Simulation and even AR tools. Providers of Digital Twin solutions include companies like NavVis and Ubisense. The organizations are able to generate smarter factories from the currently existing manufacturing enterprise.
As Computer Aided Design and Simulation continue to evolve, increasing processing power is making it possible to expand on what was started in the 1950’s. With the current ability to generate 3D models, and to provide real time simulation and process scaling, the plant can truly be visualized before it is created. The functionality will enable modelling of manufacturing lines from input to process output, and can generate multiple operating scenarios that will facilitate process optimization. Digital twins are expected to surpass their predecessors in the existing software packaging in less than five years. Anticipated process improvements are up to 10% in production efficiency.
As we continue to anticipate the emergence of the “lights out” factory, the future is definitely in robotics and AI. With 3-D CAD entire process designs will be possible. Software-Defined Manufacturing will be the baseline operation of future factories and will involve real time software instruction to a production line, once designed, and little or no human intervention once it’s up and running. Software and robotics is not perfect, with time, systems are optimized to improve their quality of performance.
Empowering the emergence and transition to the “lights out” factory are entities like Bright Machines. As a provider of AI powered software solutions, the company transforms factories with software fused with automation and machine learning. As the robotic elements in the system utilize technologies like computer vision for quality inspection processes, and servo mechanisms for motion, quality management will be seamless once fully programmed. Bright Machines optimized facilities have seen up to 60% improvement in productivity once their technologies are incorporated into existing facilities.
-
Human-Machine-Interaction: Intelligent Worker Augmentation
Automation will improve our quality of manufacturing in the years to come. While automation is an advancement that we do anticipate, there will be some tasks that only humans can perform. To bridge the gaps between the human-machine interface is the advent of Augmented Reality and Collaborative Robots. Augmented Reality is a visualization tool that factory workers can look forward to using in the field. They will also be able to provide data and instructions to the workers, so that relevant process changes can be made. Collaborative robots will be another interface that will enable humans and machines to work together to achieve process objectives.
-
AR/Wearables for control
AR devices include goggles and smart devices such as phones, watches and even other handheld devices that will enable human workers in a smart factory to engage with their automated environment. Since innovation is always accelerating, the possibility for training of employees will also be possible via these tools. Organizations such as Bosch and Magic Leap have started finding ways to bridge the gap in the current tools available to organizations wanting to implement AR. Their interface the Common Augmented Reality Platform is one that provides an interactive platform that interacts with shop floor operators and enables them to interact with machines in their environment. AR is also a great visualization tool for future changes to the factory. Astronauts use this tool before missions to visualise their launches and landings, and it is just now reaching the industrial world.
-
Computer Vision:
Computer Vision is a tool that is utilized for various industrial operations, but particularly for quality management. Companies like Instrumental, Landing.ai are emerging in the computer vision realm. As tools that are able to spot manufacturing issues and actually solve them, when flaws are found in products, the data will then be collated and the root cause of this found. Utilizing technologies such as blockchain technology, the entire process can be visualized and adjusted until the final products are as desired.
-
Digital-physical conversion: Industrial Robotics
The ability to transition from CAD to the production line was first made possible when about a decade ago, the 3-D manufacturing technology was made available to the mainstream. 3-D printing, like cellular manufacturing is one of those technologies that will enable agile manufacturing to be possible in a time where uncertainty can be the order of the day. Where continuous processes can be disrupted, the utilization of technologies like additive manufacturing, is one that will enable just in time processing and allow the creation of designs in house without having to utilize external suppliers for anything more than the raw materials for printing. Mass customization is made possible with 3-D printing.
Companies such as Mark Forged, Xometry, Maketime , 3D Hubs and CloudNC are enabling design and manufacture of products to be seamless and readily accessible to industrial entities, and even civilians who can order their kits online.
Collaborative robots, introduced above, involve the integration of workers with robotic hardware. With every transition phase there is a global concern. The concern that industrial machinery may be too large to interact with workers has often surfaced in industrial discussions. The solution to this is the development of cobots, which aim to interact with humans in a manner that is akin to human behavior. The additional argument that cobots need more data and intelligence to interact with people is also a concern. With plenty of room to grow and develop, cobots still are being developed for the market to meet the needs of the industrial realm. Companies like Hahn Automation, OnBot, Realwear and Kuka, aim to generate more units, and in the intelligence gathering process, will enable the optimization of the human-robot interface.
Everything boils down to demand and supply. With an increase in production activity, there will be an increase in the demand for future “lights out” facilities that are able to produce non-stop, without the intervention of humans. Ecommerce is on the rise, and factors such as production, and warehouse storage will be key to filling this need. Kiva Systems, Boston Dynamics and German Magazino are pioneers in warehouse management via robotics, and are currently gearing up to provide warehouses with robotic functionality that will optimize their systems for peak operations.
Industrial hardware without software is simply a shell. Once programmed correctly, the most optimized factories are possible. Industrial optimization is always at play, and organizations such as READY Robotics, Vayyar and Forge, are able to provide the best in industrial robotic software. The tools have the capability to operate via control centers that have smart phone level intuition, yet still are able to accomplish the desired robotic motion control.
-
Smart Supply Chain & Logistics
A discussion about robotic process control will not be warranted without the discussion of autonomous vehicles. One of the most exciting themes of late in the transportation world is the advent of vehicles like Tesla’s Automated Trucks, which will enable the optimization of logistics and transportation globally. What these vehicles will do, is facilitate the automatic transfer of goods, once a Bill of Lading is received by the relevant organization. With greener movement, the environmental benefits will definitely be gained. Various enterprises are currently in the phase of optimizing their vehicles, and aim to transition from initial road tests, to actual full scale operations.
New industrial technologies will require funding in order to thrive. The success of various preceding technologies is enabling that to be so. While Venture Capitalists are seeing and investing in areas such as robotics and additive manufacturing, they are also giving opportunities to organizations that are able to provide industrial solutions that improve visualization software and process hardware functionality. Venture Capitalists are careful investors and usually wait until they see certainty before they invest their funds. The companies highlighted in this discussion have managed to successfully access funding that will continue their missions of system optimization. The vision of the investment exercise is to enable the integration of the different aforementioned segments of machine and industrial optimization in order to accomplish the desired objectives of reaching a just in time “lights out” facility. The gains from this facility will be the returns that the Venture Capitalists and industrialists aim to achieve. The future is evolving before our eyes.
Conclusion
Manufacturing is an evolving field, that is always on the frontiers of efficiency and automation. The process is dynamic and will take a while in order to achieve. The manufacturing industry is often associated with their slow adaptation of technology for various reasons. The initial investments are often capital intensive. With digitization becoming an industrial standard and a must for competitive advantage, evolution will be necessary. The tools that will facilitate this change will include the ones highlighted in this discussion.