Criteria for plant layout evaluation
Proper plant layout designs are one of the important steps during the construction of manufacturing industries because material flow distance and material handling cost are affected by plant layout designs. If proper layout designs are not adopted then material handling cost and material flow distance become high. Thus total manufacturing cost and time can be increased because of poor plant layout designs. Benefits and productivity of the manufacturing industries can be increased if good plant layout designs are adopted.
Process layout, product layout and cellular layout are most commonly used layout models in the creation of plant layout designs. Process layout, product layout and cellular layout all have their features which can be used to decide how close they are from the goals of the lean manufacturing system. Here we discuss criteria for layout evaluation which can be used to determine closeness of specific layout model from the goals of the lean manufacturing system. Criteria for layout evaluation are depicted in figure 1 and explained as per the following.
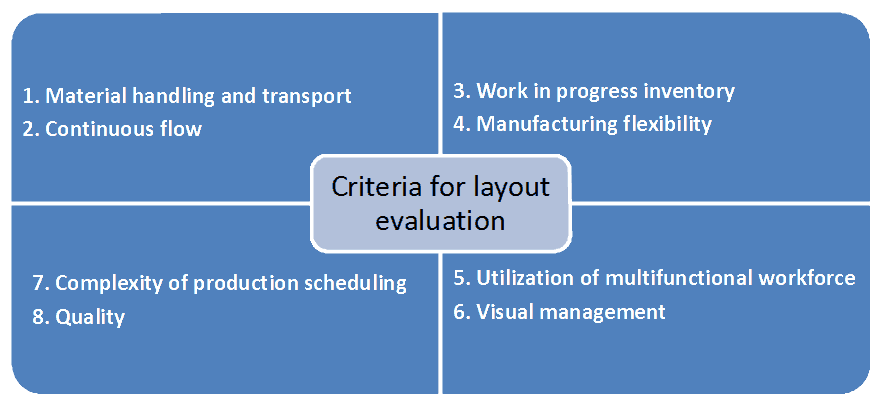
Figure 1: Criteria for plant layout evaluation
1. Material handling and transport
From the lean manufacturing point of view, effort should be made to minimize material handling and transport during manufacturing because they are just no value added activities. Such no value added activities called wastes should be removed from manufacturing processes. Thus plan layout designs should be created in a way which minimizes material handling and transport.
2. Continuous flow
Flow should be continuous from point of view of the lean manufacturing. Thus plant layout designs should be created by placing equipments as close as possible in order to achieve smooth and continuous flow of materials. Smooth and continuous flow of materials should not be achieved by unnecessarily placing equipments far from each other.
3. Work in progress inventory
Work in progress inventory is a waste from the perspective of lean manufacturing. Plant layout designs should be created in a way which removes the need of manufacturing parts in batches. Work in progress inventory should be minimized by placing equipments as close as possible and by not creating intermediate stocks.
4. Manufacturing flexibility
Needs of customers may be different for different time periods. In order to satisfy changed needs of customers, plant layout designs should be created so that both a varied quantity and a varied mix of products can be manufactured.
5. Utilization of multifunctional workforce
Multifunctional workforce can be achieved if workers can able to perform multifunction by operating multiple equipments at the same time. Operating multiple equipments simultaneously can be possible and easy for workers if machines are placed as close as possible in the manufacturing plant.
6. Visual management
Whole production plant should be clearly visible in order to properly perform various administrative activities of the production at the operational level. Plant layout deigns should be such that the production manager should have a clear vision of workers and the manufacturing system, when he/she walks through the production plant. Effort should be made to create plant layout designs so that complete steps of all processes should be clearly visible.
7. Complexity of production scheduling
If equipments in manufacturing plant are not properly arranged then in such cases randomness of flows becomes high. Complexity level of production scheduling also becomes high because of high randomness of flows.
8. Quality
High quality products can be manufactured if feedback on quality problems is faster and surer. Faster feedback on quality problems can be achieved if most or all operations occur in one area and among a small team. Continuous flow should also help manufacturer to manufacture high quality products.