Just In time as a philosophy was evolved after World War II in Japan, as a result of their diminishing market share in the auto industry. Taiichi Ohno, father of Toyota Production System (TPS) promoted the idea of JIT. Where, Just In Time led basis for Toyota Production System. However, JIT gained worldwide prominence in the 1970s.
The principle behind JIT was to produce only the necessary products at the necessary time and in the necessary quantity. It aimed at eliminating waste of all kinds by producing and supplying only when needed and not earlier. Adopting JIT allowed TPS to do away with inventory in the stores and thereby cutting out the corresponding costs. Henceforth, JIT as a strategy helped companies increase their efficiency level with minimizing the waste. This method requires that producers are able to accurately forecast demand.
Three elements of JIT
- Production Management: JIT manufacturing focuses on minimization of waste in all forms to achieve value-added manufacturing. They constantly improve their operations and procedures to increase productivity and efficiency.
- Total quality management: JIT manufacturing is an integrated process to continuously improve quality performance at every level to keep the company competitive and profitable.
- Human resource management: JIT manufacturing rests on the philosophy that equal respect to be paid for all workers, and the trappings of status are minimized; as it considers human resource as an essential part of the organization.
Traditional manufacturing v/s JIT manufacturing
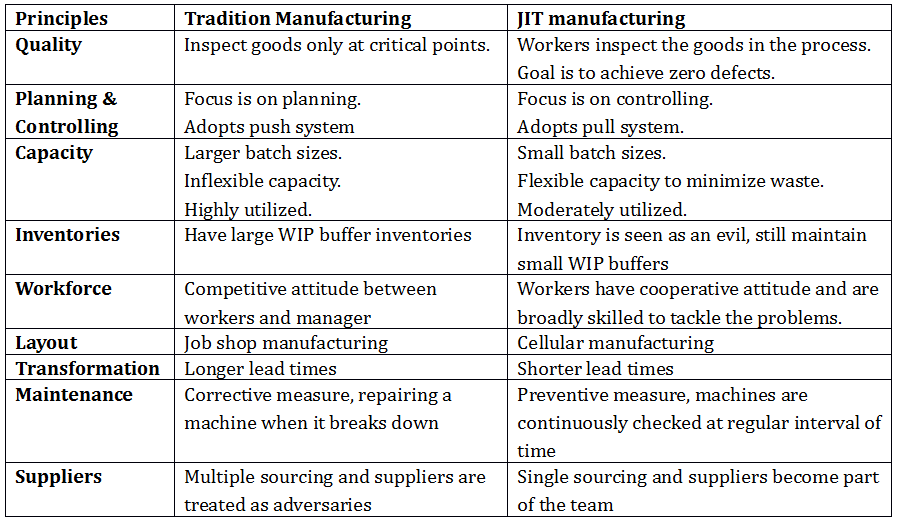
Benefits of JIT manufacturing
- Reduction in inventories, with the flow of goods from warehouses to shelves improving
- Improved quality
- Reduced storage space requirements
- Shorter lead and setup time
- Greater flexibility
- Lower production costs with reduction in scrap, defects and inventory
- Increased productivity while production scheduling is synchronized with the demand
- Increased machine utilization
- Increases focus on supplier relations
- Increases revenue to the company
- Efficiency increases as employees are trained and possess multi-skills
JIT Implementation issues
- Lack of top management support
- JIT is applicable primarily to repetitive operations
- Requires high degree of commitment at all levels of management
- Lack of formal training to the employees
- Employees resistance to change
- JIT philosophy runs on cooperation and trust
- Lack of communication within the organization about the benefits of JIT
To summarize, JIT manufacturing is a continuous improvement process that throws light on prevention rather than correction, and demands a company to focus on quality of production. The concept of JIT could be applied to any industry, such as food processing industry, shipping industry, oil industry or logistic management; where it is crucial to deliver the right quantity of goods at the right time to the right place.