There is a common misconception that the words “accuracy” and “precision” mean the same thing. To be quite fair, in colloquial speech, they are often used to mean the same thing. Both mean to hit your target, correct? Something which is accurate is also precise, correct?
Well, not quite. Let’s properly define out terms:
Accuracy: How close you hit to a single target. For example, if you have a target number of 5 non-defective products out of 5, and you hit that target goal one day, you have 100% accuracy that way. Think of it as hitting the bullseye on a dartboard. You can, of course, have less than 100% accuracy (ex if you only hit 4 non-defective targets out of 5, you have 80% accuracy that day).
Precision: The distance between at least two data points. Think of this as your consistency. You may have 100% accuracy one day, but if your data points across, say, a work week are scattered (100%, 30%, 90%, 10%, 60%) you have very low precision, where if you for example hit between 80% and 90% every day, you are very precise. Consider this “accuracy over time”.
You then end up with three intersections of these two values. These can be:
Low accuracy, low precision: Where you miss the target in an inconsistent manner (the 100%, 30%, 90%, 10%, 60% figure fits this bill).
High precision, low accuracy: Where you miss the target, but consistently hit within a certain range (for example, you hit 60% accuracy every day of the week).
High precision, high accuracy: Where you are very close to (or at) your target very consistently, Always hitting 90% every day of the week, for example.
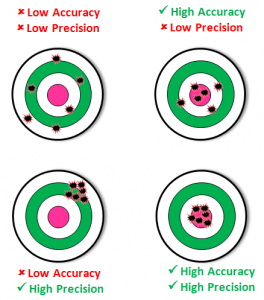
So which is more important?
Precision is the answer, by far. While accuracy is a good short term commendation, your precision is the most important factor in the long term. Consistency allows you to figure out where you are and improve if needed. Accuracy is largely meaningless if it’s something you can only achieve every once in a while; while you should always attempt to achieve your goals you shouldn’t be satisfied that they are sometimes met when your overall performance is scattershot.
In short: Hitting 80% of your goal 100% of the time is a better place to be in than hitting your goal 10% of the time and missing it by a wide, inconsistent margin the rest.
Your precision can tell you a lot of things about what goes on in your workplace over time, allowing you to identify problem areas and make adjustments accordingly. For example, let’s say you have a scattershot mix of accuracy ratings across a week (low accuracy, low precision), that previously mentioned 100%, 30%, 90%, 10%, 60% (a mean precision of 58%) figure. Look at who works the shifts where accuracy is low, and who works when the accuracy is high. Analyze how the workers on those shifts were trained, how experienced they are, whether they might be understaffed or overworked.
Then make adjustments. If you find that the employees on certain days were trained a different way, or by a different person, have them be retrained. If you have all of your senior employees working certain days, adjust shifts to create a better mix of experienced and newer employees. If too few people work certain days, or you find that the worst days come when too many people have been working overtime without rest of some such, rearrange shifts again so such a heavy load doesn’t fall on only one group of workers.
If after that adjustment you have moved, at least, to a low accuracy, high precision (Say, 70%, 65%, 75%, 60%, 70% for a mean precision of 68%) you have significantly improved (by 10%) even if your daily accuracy on some days is lowered.
From there, simple process improvement can put you on track to your ultimate goal of being both highly precise, and highly accurate.
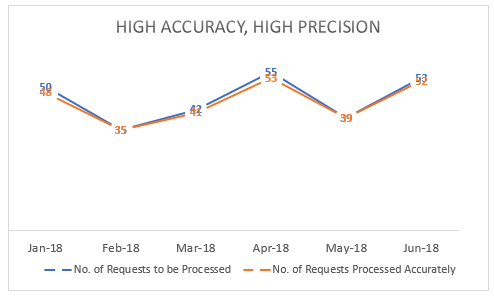
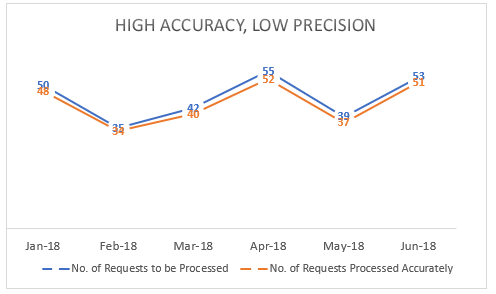
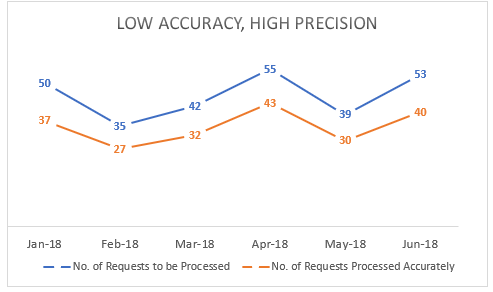