Organizations have evolved over time. Evolving from an era where persons were viewed as cogs in an industrial machine, the overall current organizational ethos is that everything matters in the journey to customer satisfaction. The customer is always king. Industrial competition supplies customers with more choices, at prices they can afford. This is the true nature of the economic machine. Organizations should simply embrace this status quo, and learn how to navigate the complicated market via a suitable strategy.
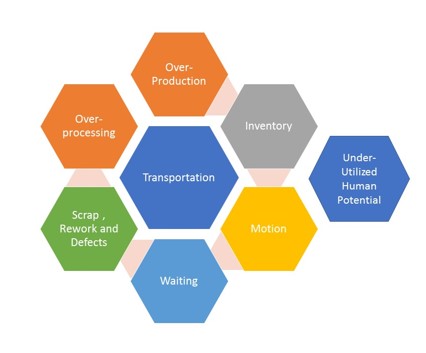
Maximizing efficiency across all operational areas is the key to organizational success. Any losses in service or product delivery can and will affect final product cost and business profitability. The key to success therefore, is to minimize any wastage in the supply chain from supplier to customer, to facilitate this objective.
“Waste” is defined as material or resources in excess of customer requirements, on the path to the delivery of a product or service.
The Lean Methodology has successfully, defined seven waste forms that contribute to operational inefficiency. These wastes are highlighted below, with appropriate examples where necessary.
UNDER-UTILIZED HUMAN CAPITAL
There is a famous adage that goes “The brain is a terrible thing to waste.” Organizations that thrive utilize their human capital to its maximum capacity. They are innovative, and continuously improving. The energy of the enterprise is always contagious, since there’s a buzz and life that keeps the employees, who actually feel like family members, engaged.
When humans are under-utilized, they are not going to give you their best. It is in the organization’s best interest to create programs that will continuously challenge the staff to accomplish newer and bigger things as time progresses. Not everyone will be influenced by money, but by the game. Intrinsic motivation will come about via an environment that generates its ability to thrive.
As an organization, it is in your best interest to tap into your human capital, because they are the future of the organization. The best examples of employee ingenuity come from entities such as 3M, which fosters a culture of innovation, and allows their employees to create new ideas and bring them to market. The Post-It was born from a culture of innovation.
OVER-PRODUCTION
One of the tenets of Lean Manufacturing is a Just-In-Time system which facilitates the minimum inventory in an ideal theoretical operation. Over-production occurs in instances where product generation exceeds product demand. The edible fats and oils industry is an ideal example of over-production. Oil consumption varies across the year due to seasonal demand. Across the year, there will be an anticipated baseline demand, which will occasionally spike as seasons such as Christmas come around.
It is in the organization’s best interest to keep enough stock on hand, to carry the organization during the peak periods. Instead of attempting to excessively ramp up production, a good way to identify the ideal inventory levels is to track customer demand, and compare it to the operational uptime. If the facility runs smoothly most of the time, the inventory levels can be kept to a minimum. Consider costing into your inventory, since the capital can always be utilized elsewhere.
INVENTORY
Inventory is a tally of the raw material progression through a process. The term is applicable to both services and products, as there is an item either physical or intangible that is being transformed via each stage. As production takes place, it is important to track the organization progress so that appropriate customer satisfaction can be attained. Appropriate inventory management is ideal to ensure that excessive capital is not being tied up. Storage also has additional costs and it is in the best interest of the management to minimize these associated costs.
MOTION
Motion waste is brought about due to inefficient operations. The car manufacturing industry has managed to minimize this waste to a science. Via assessing the best way to install individual car components such as car doors, the most efficient installation times, and production outputs have been achieved by the industry. With the advent of robotics, the precision can be improved even more, and higher consistent quality output sustained.
TRANSPORTATION
The supply chain is a critical component to sustaining operational efficiency. One way to minimize this waste is to keep all the unit operations in close proximity to each other, as well as in sequential order so that no steps are re-traced.
OVER-PROCESSING
Exceeding customer expectations beyond economic feasibility is a waste. As much as it is in our best interest to satisfy customer needs, the organization needs to protect itself. The best operational standard to uphold, is to use the minimum resources to satisfy the requirements of the customer. Appropriate process optimization strategies will minimize this waste.
SCRAP, REWORK AND DEFECTS
If a product does not meet customer specification, it is either scrapped, reworked or deemed as ineffective. This is not desired because each production pass has an associated cost to it. Built in process quality controls along the process, or blending where necessary, can help to alleviate this outcome. The advent of Quality Management Systems has helped to keep re-work and scrap at bay.
Minimizing the aforementioned process wastes, and optimizing organizational human capital utilization, will enable your organization to operate from a leaner perspective, and allow for more competitive and profitable operation.