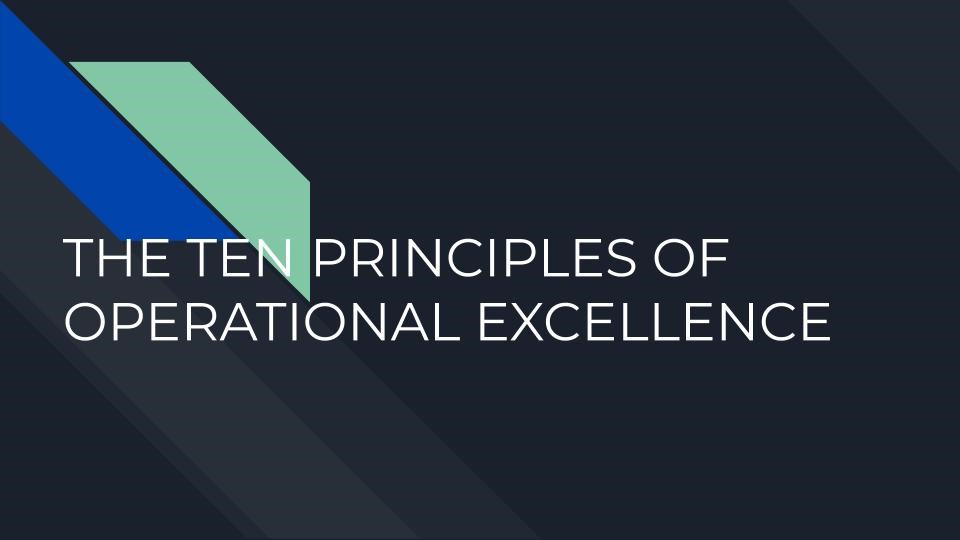
“It is not the strongest nor the most intelligent of species that survives, but the one that is most adaptable to change”. – Charles Darwin
Operational Excellence is a set of tools that industrial organizations can utilize to improve their operations. Competitive advantage is a moving target that organizations need to ensure that they are taking advantage of. There is no perfection in life, and it will be important for organizations to ensure that they are operating in an agile manner. With the various threats to a business as outlined by economic greats such as Michael Porter, organizations need to ensure that they have all of their bases covered when it comes to their internal operations.
Businesses always have areas that they can improve. The methods of achieving this objective are numerous. With Operational Excellence as a tool, there are actually a series of ten tenets that an organization can utilize to ensure that they are on top of their operational tactics for improvement.
With Lean and Six Sigma, sometimes it might help an organization to have a major event like a focus plant that will enable an organization to see an overarching set of actions that an organization needs to focus on, but alternately, just simple daily actions that organization can take will enable the desired objectives to be met. Operational Excellence actually embodies a series of gradual actions that will facilitate the change. Within the Operational body of knowledge, there are actually ten major principles that an organization can utilize in their quest for continuous improvement. With the right mindset, the appropriate strategies can effectively be implemented into your operational strategies. As an ongoing process, Operational Excellence is a tool that has an amazing ability to create and sustain improvements.
For an organization striving to satisfy its customers, utilizing operational excellence is a means that value delivery can be sustained in the operational flow. Some tenets such as quality are satisfied by the embedding of Operational Excellence strategies into the operational plans. With the right internal structure, the appropriate outcomes will naturally come forth.
Let us delve into the ten core principles that will facilitate Operational Excellence in your organization.
Principle #1: Respect Every Individual
Employee involvement in your organization is enhanced by allowing your employees to feel as if they are respected members of your organization. The more employees feel that they are empowered in your organization, is the more that they will feel inclined to actually contribute to the organization’s objectives. When there’s a need for improvements, they will be the ones who will champion your projects. If they feel appreciated, they will reciprocate the sentiments.
Principle #2: Lead with Humility
Servant leadership is the desired operating mode. Leaders of an organization are actually beholden to their subordinates. The subordinates are the ones who are executing certain critical tasks in an organization. It is in the best interest of the leadership to humble themselves to those who work for them. With the minimal airs, the leadership can then create rapport that will be a win-win situation with their staff. Loyalty will then be generated.
Principle #3: Seek perfection
While perfection, doesn’t exist, what Operational Excellence is focusing on is pressing towards a target and allowing yourself to improve towards it. It involves not settling into a mode of mediocrity, but allowing the organization to keep expanding. Set a high bar, so that you’ll keep growing and evolving.
Principle #4: Embrace Scientific Thinking
The scientific method is an analytical way of looking at your operational process. There is no perfection, and the organization must always look at ways to keep itself in a state of experimentation that will lead to operational improvements.
Principle #5: Focus on the Process
Utilize systems that keep the system as a core focus. Utilizing methods such as Daily Management that keep the system and processes visible, an organization will be able to tell if the process is performing at peak, or if it needs to implement steps to improve the process and restore it to target.
Principle #6: Assure Quality at the Source
Build quality into the process. This involves ensuring that all the quality enablers are known and managed throughout the operational process. If the enablers are enhanced at the source, there will be no need for downstream tweaking.
Principle #7: Flow and Pull Value
Maximize value in your organization’s operational flow by ensuring that processes are efficient. With appropriate system efficiency analyses, minimize waste across the entire value chain.
Principle #8: Think Systematically
Envision the entire system as an interconnected flow. Each successive department will be the customer of the department preceding it. With open communication, the ideal flow and quality sustenance will be accomplished.
Principle #9: Create Constancy of Purpose
Organizational goals must be clear and certain. With a vision, each day will have a target. There will be no ambiguity.
Principle #10: Create Value for the Customer
The customer is king. Ensuring that the voice of the customer is heard, will ensure that the organization is building those requirements into the process flow and delivering the desired results.
With these tenets, while you won’t attain the perfect organization, you will achieve an organization that is self aware and focused.