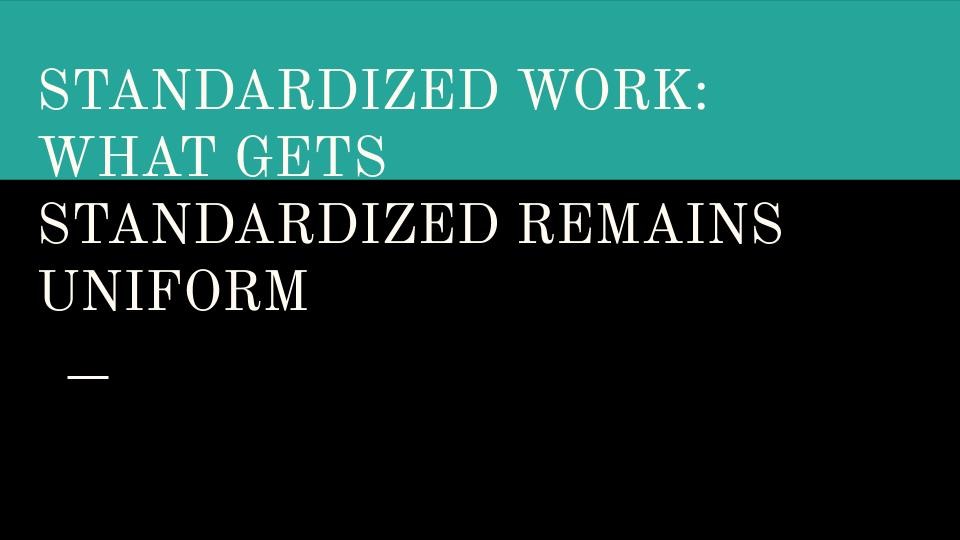
With continuous processes, standardized work is a methodology that ensures reproducibility of products, and sustains product quality. The key is to ensure that the customer is satisfied with the purchase that they make. Ensuring uniformity in the production process is the key to ensuring that production efficiency is upheld.
The combination of three operational tools in lean manufacturing will ultimately result in what is known as standardized work. Even in the advent of Industry 4.0, we still need to ensure that our automated facilities have the ability to be able to be managed by the relevant persons on hand. These relevant tools will include: takt time, work sequence and standard inventory.
From an operational perspective, these tools will be synchronized in order to ensure that they are facilitating the accomplishment of the mission of being just in time.
ADVANTAGE OF STANDARDIZED WORK
With standardized work, there is uniformity in how things are done. This provides the ability for consistency in the product output. If the most efficient ways of doing things are known, then the variation in the process output will be mitigated against. The industrial plant is a space where you want precision, in order to provide accurate estimates to the customer to let them know when their items will be available for delivery. With Industry 4.0, with the advent of sensors and technology, the relevant calculations that an organization’s needs in order to have an accurate representation of their organizations will be accessible.
Training will be much easier in an organization that does contain a series of standardized documents. If an organization is well organized and staff have access to information on their process that is aligned with the information that the rest of their team has, there will be uniform knowledge of the process across the shifts. If the plant Operator on shift B experiences a problem, they will react in exactly the same way that an Operator on Shift C will react if they were in a similar experience.
-
Increased Safety
Awareness will ensure uniform operations. There won’t be any risks incurred by inexperienced staff members because there will be.
PROCESS IMPLEMENTATION
Many operational processes are standard processes that are conducted on a routine basis. For this reason, there can be procedures written for the operation of these tasks. While operators will have the ability to make changes to the document if they see fit, during production operations, utilizing a standard makes it easier to identify if there’s a process issue. Once there is an issue, the plant can then take the time to actually conduct a root cause analysis with the intention of fixing the problem.
STEPS TO WRITING THE IDEAL STANDARDIZED WORK INSTRUCTION
When it comes to writing a standardized work instruction, the good news is…there is a standardized work instruction. We need a recipe that will ensure that the documents that are produced are actually of a quality that is matched across all operating departments. There are four primary tenets to include in your operational document.
- A process hierarchy: A process hierarchy gives you an idea of the relevance of the task at hand to the overall process. While every task that is performed in a process operation is actually relevant, the impact of an incorrect execution is one that the organization will have to weigh. For a task that is process critical, there will be additional steps to be taken to ensure that the process is done correctly. This can include ensuring that a more experienced task member does the job, or that adequate supervision is provided if the individual performing the job is a newer employee.
- A process map will be critical to the understanding of the job. It could be that the individual may need a visual of the area to be worked on, just to ensure that there is no discrepancy when the servicing of the part is to be done.
- A procedure outlining how the task is to be done. This will ensure that there is no change between one operator and the next. They will simply be in a position where they can conduct the task if an individual is out that day, or if a problem were to occur off shift.
- A work instruction – further details relevant to the execution of the job. Safety considerations should be factored into this portion of the write up, just to ensure that safety is always first.
With all the relevant details outlined, these work instructions can be stored on an online database and staff given access. If a staff member is out in the field for instance, they can simply utilize their company tools such as a tablet, download the file and proceed with the job. Having standard readily available information will be key to process optimization.