It is a work philosophy that was born as a methodology for improving and solving complex problems. Its creator was Dr. Mikel Harry, who developed it as a tool to control and decrease the variation in processes. Since then, his concept has evolved through multiple contributions to become a philosophy put into practice in the highest performance processes.
In the organizational scope were Motorola, General Electric and Honeywell who popularized the methodology, with the active participation of its creator.
What is Six Sigma?
Conceptually, six sigma can have different meanings; for practical purposes we will focus on two:
From a statistical point of view: Six sigma is a metric that allows measuring and describing a process, product or service with an extremely high processing capacity (accuracy of 99.9997%). Six sigma means “six standard deviations from the mean”, which translates mathematically to less than 3.4 defects per million.
The above means that a process that implements six sigma will stop using the average as a metric to evaluate the overall results; instead it will use the standard deviation, which represents the variation of a set with respect to its average, so that the process must comply “consistently” with the quality specifications, changing the paradigm of averaging good and bad results.
From a strategic point of view: Six Sigma is a philosophy (strategy and discipline) that adjusts processes with the minimum possible tolerance as a way to reduce waste, defects and irregularities in both products and services.
Strategy: focuses on customer satisfaction.
Discipline: Follows a formal and systematic model of continuous improvement
What is Six Sigma implemented for?
The main purpose of Six Sigma is to achieve customer satisfaction, in that order focuses on understanding their needs, collect information, and through statistical analysis find opportunities for improvement, a consistent improvement.
Once implemented and achieved Six Sigma quality control is unnecessary, since we are talking about processes with the highest levels of performance, since Six sigma allows:
Ensure quality in each job (unnecessary control).
Train people capable of improving quality.
Ensures the sustainability and profitability of business.
Design and develop capable processes, products and services.
Principles of Six Sigma
Perhaps one of the most relevant characteristics of Six Sigma and that is strongly contrasted in practice, is that quality is ensured in processes and not in inspections.
In that order quality is generated and controlled in the processes; In addition to this, Six Sigma has other principles, for example:
All staff must be trained in Six Sigma.
The Six Sigma application has a proactive approach.
Six Sigma is a systematic methodology and structured tools.
It must work from the critical characteristics to ensure all the variables of the processes.
Lean manufacturing and Six sigma = Lean Six Sigma
First of all it should be considered that Lean Manufacturing and Six Sigma are different strategies; While Lean Manufacturing has a productivity-oriented approach, Six Sigma has a focus on reducing variation.
Lean Six Sigma is then a new concept, which some specialists define as:
“Lean Six Sigma is about continuous, incessant improvement – analysis after analysis, measurement after measurement, and project after project – Lean causes products to move faster through the process and Six Sigma improves quality.”
The application of the Lean and Six sigma methodologies does not exclude other methods of improvement, it is the function of those responsible for its implementation to complement them correctly according to the appropriate approach, for example:
Procedure to implement Six Sigma
As mentioned above, Six Sigma uses the DMAIC methodology (Define, Measure, Analyze, Improve, Control), which consists of:
1. Define:
The project to be carried out is defined, generally according to purpose, scope and results; or depending on the problem, processes and objectives. Thus, the purpose and objectives of the Six Sigma will be to reduce the defect rate to less than 3.4 per million, depending on the estimated time for each organization.
Support tools: Matrix diagrams, Pareto diagrams, Process maps.
2. Measure:
Data and measurements of the process are obtained. It is usual that this phase is supported in value and observation maps. Key aspects, relevant data, should be measured and documented, considering all the variables and parameters that affect the processes.
Support tools: Flow diagrams, Process maps, Sampling techniques, AMEF, QFD, Kano model, OEE, Sigma level.
3. Analyze:
As the specialist Oskar Olofsson states:
“If statistics do not support a cause and effect relationship, DMAIC of Six Sigma does not offer a solution.”
In this step, the data collected in the measurement are converted into information; In this phase, the key causes of the problems must be identified from the variables and parameters.
Support tools: Value maps, Flow diagrams, Route diagrams, Analysis of changes, Ishikawa, Control charts, Cpk, FMEA.
4. Improve:
Depending on the main causes of the problems, the processes must be modified or redesigned. It is key to involve the personnel that is directly related to the processes, this is a fundamental step in the continuity of the improvements.
Support tools: 5’s, Methods engineering, Line balance, SMED, TPM, Kanban, Andon.
5. Control:
It must be verified that the results are sustained, this phase is the principle of continuous improvement. Improvements in the process must be ensured in order to sustain performance levels, in the same way that incremental improvements are adapted over time.
It is vital to implement information collection systems in this phase in order to constantly compare the indicators of the improved process with the parameters identified in the “Defined” phase.
Support tools: Andon, POE’s, LUP’s, Training.
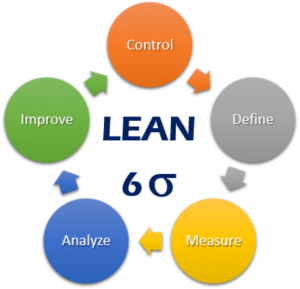
Six Sigma Structure
As has been emphasized throughout this article, Six Sigma is a powerful tool, however its impact depends largely on its structure. For the implementation of Six sigma there are different levels of training, depending on the role that each person occupies in the development of the methodology.
-
Master Black Belt
The Master Black Belt is the trainer of the Black Belts; To access this level a professional must demonstrate great experience through results in complex projects. This distinction is characterized by prestige and leadership.
-
Black Belt
He is an expert in Six Sigma philosophy tools. Its function is to lead teams implementing the methodology; he has studied and demonstrated through results his experience in projects of waste reduction and process variation.
The Black Belt is usually an internal consultant, to access this level a professional must receive training between 120 and 150 hours.
-
Green Belt
The Green Belts are employees of any level of the organization, who do not lead or dedicate 100% to the development activities of Six Sigma, but who know the methodology and who have been involved in the implementation of the implementation of Six Sigma projects.To access this level, an employee must receive training between 48 and 72 hours about the methodology.
They are usually supportive elements and can lead small projects.
-
Sponsors
They are executives who know and most importantly, believe in the benefits of Six Sigma tools. Their role is of vital importance because they are in charge of sponsoring the training programs and giving the necessary relevance to the program within the company and from the highest levels of management.
-
Champions
They are managers of a high level in the organization who allocate resources and means for the training and implementation of projects of the Black Belts. As such they should receive training regarding the methodology.