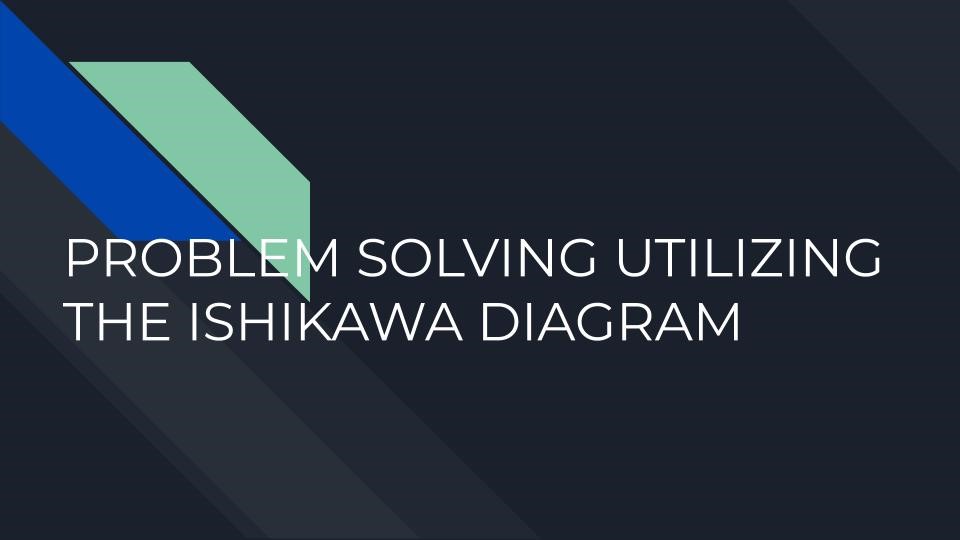
“Successful people ask better questions, and as a result, they get better answers.” – Anthony Robbins
The Deming cycle is a process that involves creating a feedback loop that is centred on your industrial process. It is an operational activity. Knowing that there is no perfection, Operations managers ensure that the appropriate time allocation is available for any system authorities to correct any underlying issues that may arise in the process of delivering the desired customer requirements.
Since operational processes are not perfect, on almost a daily basis, there will be a parameter that is off target. When a process issue is identified, it is ideal for a systematic process to exist that facilitates the appropriate elimination of the hindrance. Utilizing lean systems, it is best for these issues to go through a five step process of Issue Identification known as an Ishikawa or a Fishbone Diagram. Designed to fit into the daily management systems that we are so used to in the Lean System, the Ishikawa Diagram is the ideal way for a system to work through problems and identify their root causes.
With appropriate root cause analysis, a stable and efficient process operation will be attained throughout the process operational cycle. With the appropriate foresight, critical action can then be taken to ensure that root causes are appropriately eliminated. In the course of an operation, the root causes of the process discrepancy will indeed vary, but it is in the systematic process that all solutions will ultimately be attained.
The root cause analysis system also provides an appropriate means via which the issue resolution process can be appropriately analyzed and documented for future learnings by the process team. With each process iteration, the process becomes easier and the completion activities are completed in a faster time frame..
ROOT CAUSE ANALYSIS:
Via the Daily Management process the following five steps are implemented in an appropriate Problem Solving System:
Issue Identification: When an issue arises during a process management activity, the first step is to log the issue so that it can be further discussed by the relevant assessment teams on the process team during a problem solving session.
Issue Analysis: Using the appropriate tools, such as a problem solving, the challenge at hand can be appropriately analyzed in terms of severity of impact on the current process activities.
Issue Evaluation: Analysis of the problem often leads to its root cause. Typically using a method such as a Fishbone Diagram, or a Pareto Chart, the severity of the identified problems from the analytical phases of the project can be compared with each other. The largest impactors will influence the creation of an action plan that will rectify the issues at hand.
Action Implementation: The project team is challenged with the task of completing the prescribed project for the purpose of improving the organization’s future operations. The project issue is a hindrance to project completion and must be rectified as soon as possible, or else the project can run into time and cost over-runs. An appropriate project action completion checklist is created, and acted on over time.
Monitoring and Review: As with all lean processes, what gets measured gets managed. The relevant responsible parties will respond to the project manager as the hindrances are overcome. This activity concludes or feeds into the feedback loop of the Issue Management System.
Issue Management System Best Practices and System Conclusions
The lean system is a continuous feedback loop that ensures that the appropriate system targets are being met. When there are critical challenges, or issues seem not to be progressing past a critical point, systems must be put into place that will ensure that the appropriate escalation in a chain of command can be implemented. This is akin to a reaction plan.
A suitable example includes the building of any commercial system such as a pump system. If a lower level operator cannot manage the process of constructing the system, the matter would then be escalated to the system mechanical engineers to facilitate the appropriate fixes. With the higher level understanding, the system mechanical engineers will then be able to facilitate the problem solutions and progress the project. The pulling on the chain of command, ensures that the problems are always talked about until they are resolved.
FISHBONE DIAGRAM PROCEDURE
The Ishikawa (Fishbone) is designed much like the name suggests. A series of causes that are feeding into a final outcome. This document is a scientific means of ensuring that all aspects of a problem are assessed by an Operational Team. Factoring in the elements of Material, Measurement, Machine, Method, Environment and Employee, the differing contributors to a problem are discussed. This is designed to be a brain storming type exercise that will ensure that the critical problem is being thought of from various perspectives.
Utilizing either a board, or a pre-printed sheet, the critical sections are discussed and noted. Once all the possibilities are highlighted, data is then utilised to validate the possible root causes of the condition. In the case of the pump system above, the various contributors such as feed flow, discharge flow, packing, fluid viscosity, age of the pump will be laid on the board.
From the experience of the process team, the root cause will eventually be identified. Once this is accomplished, the team can then go through the process of devising an action plan and implementing it. As a very scientific method of problem solving, the Fishbone diagram is ideal for identifying root causes due to its wholistic view.