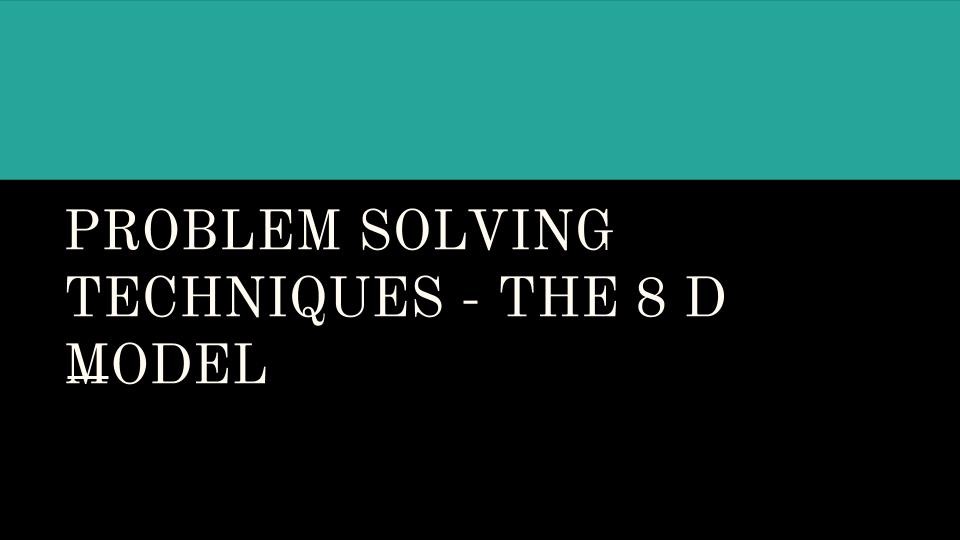
“Rough waters are truer tests of leadership. In calm water, every ship has a good captain.”- Swedish proverb
Industrial operations are designed to have a stable flow. An industrial plant is designed to be one of the safest places on Earth. Every vessel is designed with built in mechanisms to keep its intended process solutions within, and to achieve the objective of meeting production targets. In the process flow, a company will identify the voice of the customer and then ensure that its operations are tuned to achieve the desired objectives.
Every process control engineer, envisions a day when a plant will pretty much run itself. While some systems are completely autonomous, human intervention will often be needed to correct problems, and even to facilitate maintenance activities. While Daily Management as a system is a medium that will identify when production system parameters are off target, there are additional tools in the industrial sphere that will allow operations teams to identify problems in their day to day operations and then take the relevant actions to solve the problems.
There are tools that organizations can utilize in their operational realm to facilitate problem solving. The eight disciplines model is one such tool that a company can utilize in its quest for an all green operational board. An operation’s manager’s favorite colour is green, meaning that all operations targets are being met, and that being the case the plant can then turn its attention away from firefighting, and focus on systems optimizations.
An all green board is not an impossible task, but it is in essence a rare occasion. Problem Solving is an activity that is always ongoing, and as a result, it is in the Operations Managers best interest to ensure that the teams on the plant are doing the activity, and enjoying the method that they are utilizing to achieve their objective of identifying a root cause to a problem so that it can be eliminated.
The Eight disciplines (8D) model is one tool that will make the problem solving exercise a fun one. As a tool that is utilized for quality management in particular, it is finding itself evolving into other spheres that require system wide standardization. With 8D as a tool, root cause analysis will be accomplished and the relevant actions can then be taken by your maintenance team in order to rectify the issue at hand. As with all industrial systems, it is actually easier to utilize a case study.
HOW TO USE THE 8D SYSTEM
Case: Let us assume that on an industrial morning, a morning meeting was held. The meeting identified that a critical parameter (heater exit temperature) was below the target for three days straight. The three day trigger is an indicator that a problem solving exercise should be undertaken. The team usually loves to utilize a Fishbone Diagram, but today based on the nature of the exercise, they thought it would be a good idea to try something new and utilize the 8D system. Here are the steps that would be utilized to determine what went wrong in the system to cause the current outcome.
- D0: Plan – Plan a meeting to discuss this problem. In a department’s schedule, there should be a set time each week for problem solving. For problems that are absolutely critical, engineers and maintenance teams can problem solve on the day they occur, but for longer problems they can wait till the scheduled problem solving time to be tackled.
- D1: Identify a team – Departments usually assign individuals to manage problem solving exercises. Chemical process engineers tend to lead meetings and they are supported by reliability engineers and the operational staff who are responsible for particular equipment that is affecting the issue. In this instance, the heater is malfunctioning, so the operator who puts the heater into and out of service will be handy to have in a meeting.
- D2: Define the problem – As best as possible, utilizing the identified problem definition tool, identify what went wrong. It is always useful to identify the day and time that the parameter went off target. A good example includes: “At 8 45 pm on Thursday, April 4 2019, it was identified that the heater exit temperature on the T3 heater was below target. The problem was identified by the control system operator, who then informed the operational manager that there was an issue.”
- D3: Develop interim containment plan: This step will be a step that the organization can then decide on during the meeting. In this instance, since the heater exit temperature is low, a quick action such as increasing steam addition or increasing the flow of a hot transfer fluid can then be facilitated. Where possible, take the time to isolate the problem if it’s one that won’t affect the process.
- D4: Determine, identify, and verify root causes and escape points. In this instance, a detailed root cause analysis would have identified what the root cause of the problem is. Utilizing the 5 Whys as a system, all the possibilities will be identified and the root cause determined.
- D5: Choose and verify permanent corrections (PCs) for problem/nonconformity. The majority of process corrections are adjustable on a shift. In some instances however, there are instances where plant shutdowns or equipment downtime will be required for the rectification. If a longer fix is required, the entire plant may need to be aware so that departments can adjust to a flow change during the fix.
- D6: Implement and validate corrective actions. During this instance, the actual rectification will take place. For the heater above, a heater change or a heater cleaning may need to be done. A few hours of maintenance may be necessary. Since most activities are routine, the operations staff can comfortably inform the plant how long the job will take. In time, you’ll realise that most things aren’t new.
- D7: Take preventive measures. Preventative measures will be identified during the problem solving exercise. In this instance, it may be identified that the heater was not maintained on time. That being the case, the fix would be to ensure that the cleaning schedule is stuck to.
- D8: Congratulate your team. Periodically thank your team for achievements. Tie their achievements to incentives, so that they’ll keep wanting to identify problems and champion the initiative to keep the plant as efficient as possible.
As a tool, the 8D model is definitely worth implementing in your operational system. It is the ideal tool for ensuring that problems in your daily management system are being addressed in a systematic manner. Order is the ideal way to operate in a plant.