Kanban within The Process
These are used to establish the sequence of the transport line within a process. They are used in the lines of assembly or in a multiple production of pieces, subject to small changes of the die. They are common in production line processes.
- Kanban sign
The kanban signs are used in a single line or in a process where the equipment where the machines are used for various types of pieces requires some form of a longer time for die changes.
The kanban sign of operating instructions in batch production processes, usually referred to as triangular kanban.
Kanban between processes
In the assembly line, the pieces must be collected from several previous processes, such as machines, presses, paints, nickel plating, etc.
In addition to the kanban of production instructions necessary to develop the operation of the assembly line, other instructional kanban are required to separate the pieces from the previous process. The kanban between processes provides this type of instructions.
Kanban between suppliers
These are essentially the same as the kanban between processes. The only difference is that the previous process is an external company.
Operations
For the kanban system to work effectively, certain preconditions must be met. In addition, operations rules must be formulated.
Let’s examine the following:
- The definition of the area of insufficient parts.
- The operational method of a kanban within the process and a kanban between the process.
- The operational method of the kanban sign.
Definition of the area of insufficient parts
creation of a location code and administration shows an example of how kanban refers to the location codes in the assembly line in the plants.
The assembly lines are divided according to the flow of vehicles: TRIM I, CHASSY, TRIM II-a and TRIM II-b
The assembly is also divided into the RH side and the LH side and are subdivided with a detailed numbering.
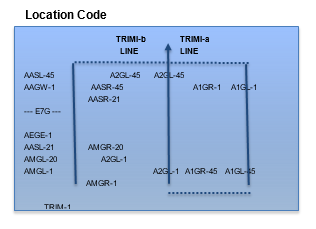
The previous image shows an indicator plate. We must consider the location code:
- One line TRIM II-b, Side RH;
- Location code number 35
The indicator plate uses color divisions to prevent a bad reading. Special shelves or flow windows are installed for small parts; so employees can quickly locate them as needed.
This type of indicator plates will make it easy for everyone to find the location code or location. Simplifies the transport of parts, and eliminates the transport of the wrong parts, and the deficit of parts
Display Location Board
Location shown on the process locator in each line

Name of the process color code
Information display on the flow shelf.
The figure shows an example of the letterhead of the flow shelf on the side of the assembly line.
5 types of information are written; numbered from 1 to 5 on the flow shelf
- The name and the missing area
- The name of the provider
- A number kanban; or the simplified part number in 3 digits
- Cycle kanban
- The total number of treated kanbans
The first point of information, the area of the shortage, must agree with the location code of the indicated plant, or the location mentioned previously.
The missing area should be shown on each line and should match the missing area of the flow shelf. If the area of missing parts is changed; The display of the flow shelf should be changed. Observe the following image.
Letterhead of the flow of the process
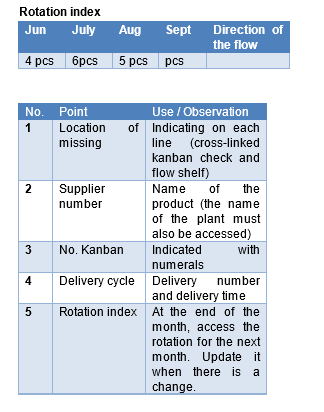
Below we will show an example of the missing area in a flow shelf in the assembly line.
The letterheads are shown in the showcases; the same pieces are always placed in the same place on the flow shelf, thus preventing incorrect or missing pieces.
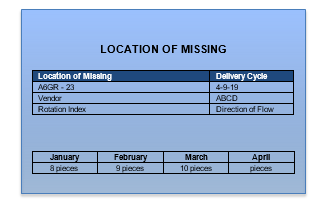
Kanban for Provider
This kanban is attached to each container with a certain number of types of parts. This type of kanban has 12 points of information:
- Location or location code
- Frequency of delivery
- Provider’s name
- Number of kanban
- Part number
- Rear number
- Number of the piece
- Type of vehicle and quantity
- Type of box rotated
- Capacity
- Identification of the area of shortages
- Received
Any change to this information requires a revision and change in the kanban for suppliers.
Next we will show the path of kanban circulation between the process and the kanban operation in the process, using an example where the previous processes are process line X, Y, Z and the next process in the assembly line.
As we mentioned above, the process lines X, Y and Z in the previous process; they have an inventory of finished parts, this is warehouse 10. There is also inventory 5 and one side of the assembly line of the next process.
The kanban in the processes; they are attached to the boxes of a quantity set, for each type of parts in the store 10 similarly, the process is linked to one side of the warehouse area line 11.
While using the parts stored in the assembly line; the kanban in the process; attached to the container is placed in the information kanban 1 at a specific time, or when a certain amount of specified remnant is achieved, the kanban is collected between the process and the transport members, they go to the previous process to collect the parts as is instructed in the kanban by taking the empty boxes 7.
Transport members go to finished parts 5 of process line X.
In current use, the kanban in the process attached to the boxes of the separated parts is put in the information of the instructions of the process 4 and the kanban between the process brought to the storage area is united with the boxes of the parts. Any empty box returned is printed in its specific places.
Transportation members go to the subsequent warehouse area and separate the parties in the same way.
In the process line, team members produce as many applicable parts as are specified in the kanban in the process taken from the kanban information of the production instruction.
If there were multiple kanban in the process in the information, the production of the process line should be processed, in the order in which it is placed in the information.
Even if several Kanban require the same parts, these parts can not be produced together in a long production line.
In the flow of kanban in the process, down the production line with the parts, and after the parts indicate that the kanban has been completed, the kanban are attached to the boxes of the parts and these boxes are accommodated in the storage area 8, as shown below.
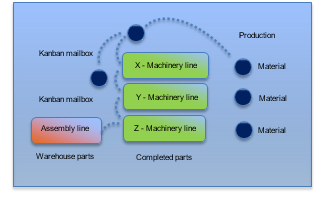