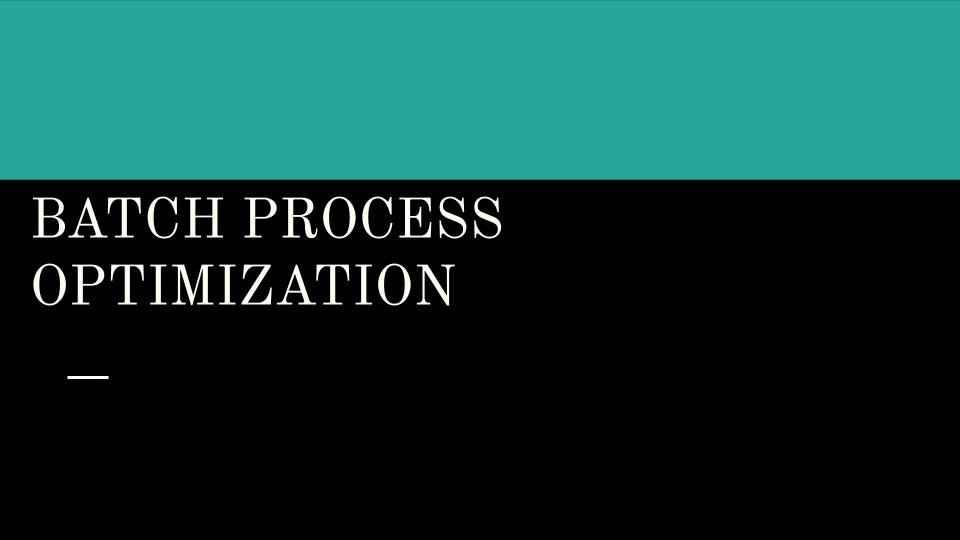
Relative reductions in economic activities may have you reconsidering how it is that you operate your industrial processes. If you were operating in an industry that is predominantly continuous, you may want to diversify some aspect of your operations in order to ensure that you are able to meet your production and profitability ratios.
Within the industrial realm, batch processes are those small operations that do pose advantageous in a time where production demand is uncertain. The beauty about batch process systems is that they are small scale, yet high value productions. Just find that right market and you are good to go. In a time where health is a concern, biologics is a sphere that we can venture into boldly. When working with such systems however, it will be highly critical that the control of these systems be in tune and up to date. In this article, we will delve into the aspects of the operations of a batch process that will enable your organization to better control the unit. With the potential to increase your ability to increase your production output in a batch format, knowing what to do in order to identify how best to optimize factors like yield and quality will always be at the forefront of your operations.
What happens in batch processes?
Batch processes are like a one pot meal. The right combination of everything from temperature, feed composition, pH and process volumes will be critical to achieving the right results. During your operations, you will then take the time to actually ensure that the unit is set to accomplish the desired objects that are desired in your operational and research plan. Since multiple parameters are important in batch process operations, it will be important for the control system to ensure that it is able to manage these critical parameters. Appropriate system sequencing will be needed in order to achieve these objectives.
As the world is moving towards biologics, product quality will always be king. The right recipe will definitely be the one that will generate the highest returns. Getting it right will be the challenge.
Knowing that process control, part of the evolution of Industry 4.0 and its pillars, will be enabling manufacturers to actually improve the quality of output, with the appropriate process conditions we are at a point where repeatability in batches is now possible. With minimal variability, the appropriate downstream quality requirements will be met. What then can batch processors ensure is in place to keep their operations going? Here is a list of some operational best practices that can assist in ensuring that quality is maintained in a smaller operation.
- Optimize your process tools. The use of the appropriate control meters will ensure that the adequate measurements are being accommodated for inside in the batch process reactor. For liquid feeds for instance, the right fluid flow meters will enable the accurate dispensing of the products into the unit. With the right measurements, the appropriate reactions can be facilitated. Additionally, for the parameters that are critical such as temperature, pressure, ensure that the probes and sensors are adequately calibrated, so that there’s no discrepancy in the readout. Batch quality can be affected by something as simple as an inadequate reading.
- Adjust your feedstock. Where possible use substitutes for some components that can be substituted. Formulation variations might be easier with one solvent versus another for instance, or there might be preferential reactions and formations to your final product in the new solvent.
- Synchronize unit operations where possible. This will save time, and also eliminate product loss due to transfer from vessel to vessel.
- Automate all processes where necessary. Human error is real, and it is possible to minimize it via the utilization of automatic dispensers that are well calibrated.
- Use data analytics to your advantage. Where possible you can monitor parameters such as crystal size distribution, batch repeatability and predict reaction endpoints. With the data that you collect for each run, you will be able to visualize the process and see how the reaction and its parameters are operating with time. Data analytics is the new oil, and with a few tweaks, you can actually conduct some virtual experiments based on the physical properties of new materials that will let you know if your current formulation is correct.
Industrial strategy in uncertain times is one that we need to carefully manage. As the saying goes, we can’t control everything, but at least we can learn to master that which we can control. As industrialists, we must be nimble in our operations in order to ensure that we are on top of competitive advantage. We can’t just rely on one thing in our lives.