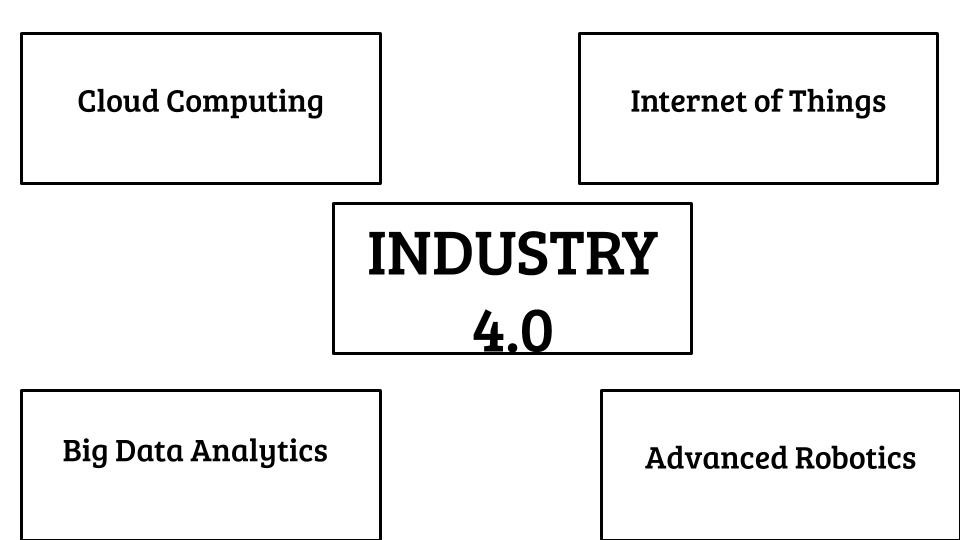
“Any skilled engineer can take control remotely of any connected ‘thing’. Society has not yet realized the incredible scenarios this capability creates.”
– André Kudelski, Chairman and CEO, Kudelski Group
Digital disruption is a phenomenon that is changing the way that industrial systems operate. The vision of an automated world is evolving in all aspects of life. In the manufacturing realm, manufacturing systems are not exempt from the evolving nature of automation. From robotic systems in the manufacture of smart cars, to the automatic process control of batch process systems manufacturing systems are well on their way to improving the quality of our products and services in the near and distant future.
Industry 4.0 is the current wave of the industrial revolution that we are now facing. As a digital transformation of the manufacturing sector, automation and data exchange will be critical to ensuring that manufacturing standards are upheld. In the Plan Do Check Act (PDCA) cycle that is associated with Lean Manufacturing, it is always critical to ensure that the appropriate quality management principles are in place, and having the means to sustain an appropriate feedback loop for process data is facilitated by Industry 4.0.
The umbrella of Industry 4.0 covers various themes including, but not exhausted to:
- Smart Sensor Utilization
- Advanced Robotics
- Big Data Analytics
- 3D Printing
- Augmented Reality
- Cloud Computing
- Location Detection
With the advent of Smart Sensor Technology, we are well on our way to an evolving Industrial Internet of Things that will make our lives that much better. In the discrete and process manufacturing realm, the gains are being experienced in desired ways. Industry 4.0 is set to be a major wave in the evolution of the manufacturing sector. What you can anticipate as a production manager is:
- Advances in automation in all spheres including the pharmaceutical sector
- The bridging of the physical and digital world through the linking of the cyber world and the physical world
- Evolution of Industrial Process Control systems from traditional legacy systems to advanced systems that integrate all aspects of the production system via the advent of sensors in all aspects of the production process. As industrial processes evolve from batch processing all the way up to continuous processes, manufacturers can feel assured that process decisions can be made in real time, and implemented as desired.
What Industry 4.0 facilitates more than ever, is industrial decision making. Competition is a moving advantage, and it will be critical more than ever for individuals to ensure that changes to process systems can be made. With the industrial complex facilitating just in time processes and enabling the minimization of storage and inventory costs, it will be critical for companies to be able to adjust their operations to match their operational desires. Real time process control and monitoring will be key to ensuring that factories remain in their just in time process operating mode. As operational costs and resource optimization is enabled, companies will comfortably be able to scale up and scale down as desired.
Digitization is a powerful force in the globe, and industry is no exception. Companies should leverage:
- Data analytics to ensure that maximum efficiency is facilitated and efficiencies optimized on multiple process levels.
- During kaizen and continuing process optimization, appropriate decision making can be facilitated due to the appropriate system data being available via system sensors. With end-to-end information systems available across the value chain, opportunities can be seen and where possible, the company services and business models can be optimized.
Organizations need to ensure that they understand their value chain cycles in or to understand the mainstream flow from their suppliers to their customers. During a smart manufacturing cycle, the entire process flow from materials sourcing to the delivery room can be traced.
CUSTOMER FOCUSED MANUFACTURING
The customer is always king!! In a time, where it is easy to find alternate suppliers, manufacturing companies need to figure out how to attract, keep, and sustain their customers. Industry 4.0 tools are the primary tools that will facilitate programming the implementation of the voice of the customer into the production patterns. The Quality-Cost pillars will ideally be realized and organizational profit targets be realized. Innovation is the key to process success and customer satisfaction.
Business as usual…will require Industry 4.0 tools. As companies evolve via innovative efforts in all aspects of their operating systems, with a focus on implementing a fusion of sensor networks with process control networks, companies can transform their companies with minimal efforts. Best practice companies are always at the top of their fields.
One key thing that you can focus on as a production manager is identifying the key producers in your field, and identifying how their sensor networks operate, and integrate with their control systems. Legacy systems are phasing out…so ensure that you are upgrading your control systems with Industry 4.0 technologies. Companies like Honeywell and ABB are always available for discussions on upgrading your systems to integrate Industry 4.0 into your operations.