SMED is an acronym for the lean production method – Single Minute Exchange of Dies. Developed by Shigeo Shingo, a Japanese Industrial Engineer, the methodology provides an efficient and timely transfer from one product to the next in a manufacturing process. This rapid transition facilitates the optimization of the available equipment in a production facility. A continuous process under the principles of SMED, can quickly be converted into a customizable job-shop hybrid as the external demand requires. Process flows are improved and product quality is also sustained via this methodology.
SMED has the potential to produce a striking reduction in system changeover times, with the ability to reduce these times to a single digit minute order of magnitude. The primary objective is to average less than ten minutes during changeover. The relevant process being optimized is dissected into its finer elements, and potential for waste is eliminated via appropriate methods.
SMED Benefits
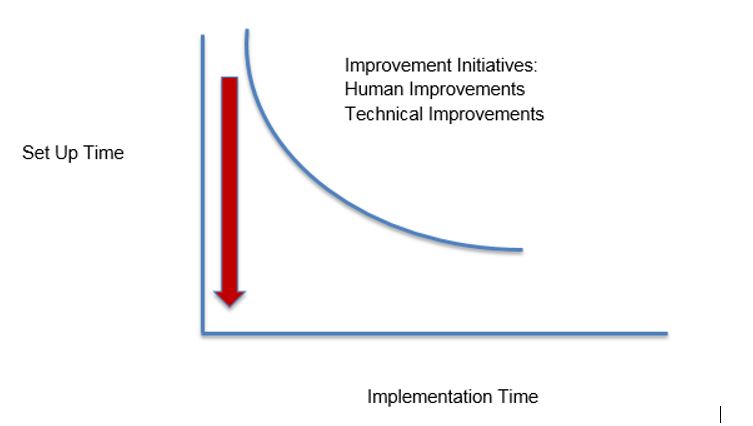
Image 1: Implementation Time Optimization Curve
Image one above, has a detailed outline of the SMED improvement process elements, as well as the associated time reduction benefits accrued from the implementation of both human based, and technical improvements. The downward transition in setup time is exactly what is expected by the organization as it implements the outlined system best practices. If an organization successfully implements SMED as prescribed, it can expect the following outlined benefits. These benefits are by no means exhaustive, but they contribute to the bulk of the gains attributed to the SMED methodology. These gains include:
- Guaranteed cost savings due to reduction in equipment downtime. If the plant is continuously operational, the quantity and value of the production output will increase, justifying the implementation of SMED.
- More product changes are facilitated in a Just-In-Time Manner. Flexible Scheduling facilitation allows continuous processes to be converted into job shops and facilitate more customized production output.
- Reduction in inventory due to Just In Time production facilitation.
- Product Quality Optimization. Tighter tolerances in die exchanges ensure that less wastage on production lines exists.
NASCAR as an example, is an excellent representation of the vision of SMED. Team effort facilitates tire changes in less than 15 seconds. Parallel execution of tasks facilitates this outcome, and integrates both internal (stopped equipment needed) and external (online equipment facilitated) elements to facilitate the target outcome. When properly executed, the relationship between all the elements facilitates a real transition between the process before SMED was implemented, and after. What is obvious, is the facilitation of changeover time optimization, by the integration of parallel teamwork executed on both internal and external elements. By facilitating these process changes, more work is done in less time, and the process uptime is facilitated.
SMED Pioneers:
Toyota is the founding father of many of today’s Lean and Industrial Optimization Methodologies. In some of their original car manufacturing processes, die changes on their vehicle body parts systems were taking extensive periods of time. The system complexity required tight tolerances, in order to prevent production losses due to deformed products. As a result, meticulous change processes existed, which lasted between twelve hours to three days. Industrial engineering assessment was able to facilitate process optimization down to 10 minutes per die.
These process changes were due to technical improvements, as outlined in Image 1, which reduced human error, and improved die change quality. Toyota was the pioneer of Just-In-Time Manufacturing, which facilitates the reduction of process inventory. Excess inventory ties up capital, so process optimization helped to eliminate that waste, and optimize business cash flows.
Attempt any of the aforementioned suggestions, in an appropriate SMED assessment, and see where your process efficiencies and cost savings improve. It is an ideal process tool to keep you equipped for the changes in industrial efficiency requirements.